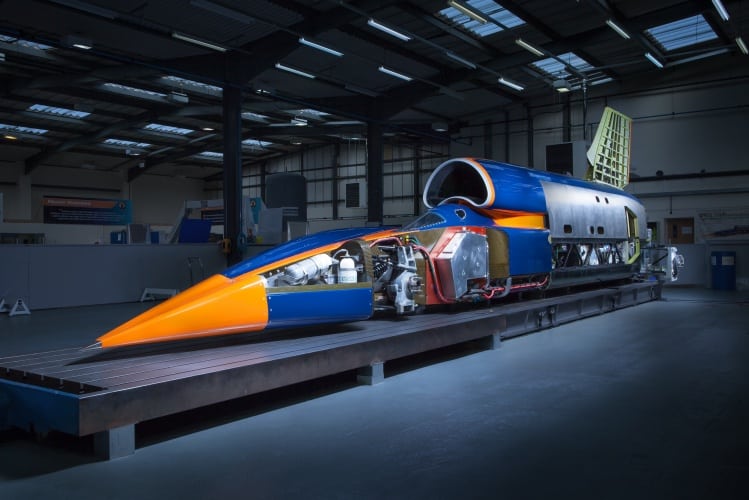
The first time I visited Bloodhound SSC was in 2010. I’d just been to see some pioneers of 3D printing at what was then EADS Astrium’s technology campus just outside Bristol, and I made a quick side-trip to talk to the project’s chief engineer, motorsport expert John Piper, to get the low-down on the project.
There wasn’t much to see. Bloodhound’s HQ at the time was near the Bristol city centre, close to the SS Great Britain, and incongruously a few units along from Aardman Animation. I remember commenting on the irony of a building already known as the Doghouse being so close to the home of Britain’s favourite plasticene dog, Gromit. The only hardware in the building was the EJ200 jet engine that forms Bloodhound’s primary propulsion system, and whose acquisition on loan from the MOD was key to the whole project. The walls were, however, plastered with posters showing the car speeding along the desert, a rooster-tail of dust in its wake. Piper was a little apologetic; the project had only been going for 18 months, he said, and the car really only existed virtually
And yesterday, more than five years later, I stood chatting to Piper’s successor as chief engineer, Mark Chapman, next to Bloodhound SSC itself.
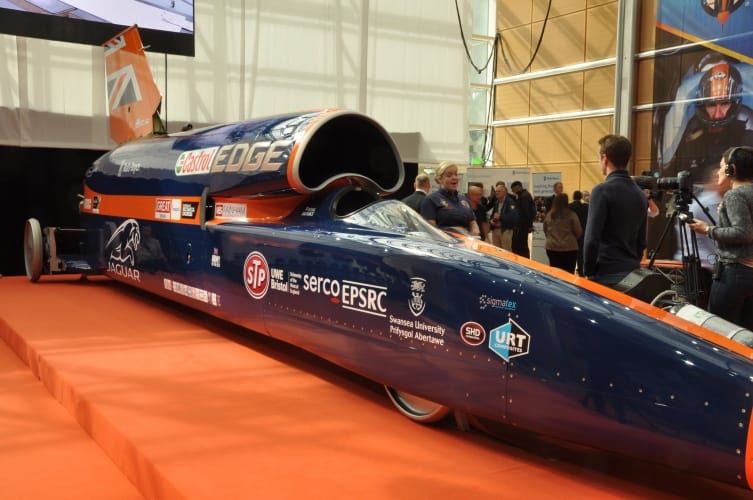
As we’ve mentioned on the website, the Bloodhound team has brought the near-completed car to London’s Docklands to make its public debut. Over the next two days, 8000 members of the public will troop into the East Wintergarden, an arched, glazed space just over the road from the main Canary Wharf tower, to look at the needle-nosed vehicle that, its team hope, will break the land speed record twice on the dried lakebed of South Africa’s Hakskeen Pan: aiming for 800mph next year (exceeding the current mark of 763mph, set by Bloodhound driver Andy Green in the same core team’s previous vehicle, Thrust SSC, on 15 October 1997); then, after a return to the UK for analysis and refitting, going back to Hakskeen in 2017 to try for the biggest increase in the record’s history, to 1000mph.
Over the intervening years, I’ve seen Bloodhound under construction several times at the team’s new, larger headquarters near Bristol’s western docks, but it’s a very different sight now. It’s not quite complete: mechanical engineering design lead Mark Elvin told me it’s about 95 per cent there. The most visible sign of this in Docklands is that the panels on one side of the car have been removed to the public can see the jet engine, fuel tanks and ancilliary systems, including the pump for the rocket oxidiser and the V8 Jaguar engine that runs it. One side of the soaring tail is also missing, revealing part of the network of 500 sensors that will monitor airflow over the car and strain on its frame as it careers along its track. The car also doesn’t have its final airbrake panels, the aerodynamic winglets that will sit behind the front wheels and on the tail, or its strake (the long ridge that runs along part of the top of the car from the root of the tail; in Bloodhound, it houses some of the car’s electronics, including its wireless modems).
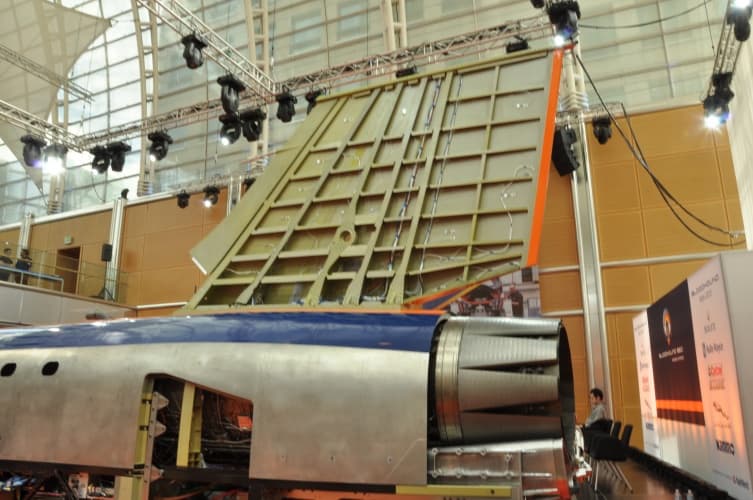
Even so, the car has a presence very different from the full-scale plastic model that’s been touring schools and exhibitions for the past few years. It seems larger; not just because of the full 2m height of the tail, which on the show model was reduced so it could fit through doors. ‘It’s a more massive feeling; in the flesh you’re much more aware of the size and power of the thing,’ commented Mark Chapman, visibly proud of the achievement of his team.
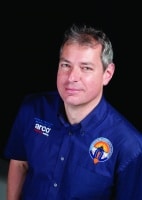
That sense of pride was palpable yesterday. The co-ordinator of the involvement of the Royal Electrical and Mechanical Engineers (REME) on the project, Major Oliver Morgan, told me that one team member, ‘a big burly bloke but I can’t tell you who,’ had broken down in tears at his first sight of the car in the hall. Elvin added that project director Richard Noble, whose famous gift of the gab has been instrumental in securing much of Bloodhound’s funding, had been rendered completely speechless (though judging from my brief view of Noble at the event, he got over it).
For Morgan, Bloodhound represents the UK’s undiminished ability to take on cutting-edge engineering projects. “I overheard someone saying this morning that we used to do things like this, and I went up to him and said, ‘Stop. We still do this, we’ve always done this and we’re bloody good at it.’ This is a milestone; it’s part of our national story.”
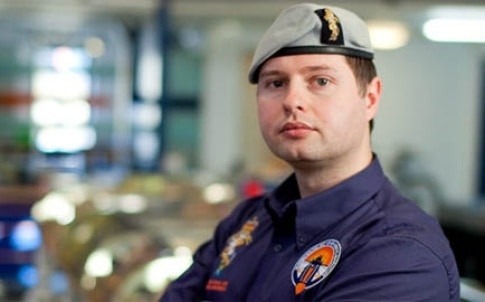
The team’s confidence is armour-plated. You will never hear anybody even entertain the notion that they won’t succeed in breaking the landspeed record, even though the project still needs to raise in excess of £10m. “That’s so we can finish the build programme and run the car in the desert,” Elvin said; part of the reason for the exhibition this weekend is to attract new sponsors. “The fact that we’re doing two record attempts works in our favour,” Elvin continued. “When we come back already holding a new record, it’ll prove our capability and attract new companies who’ll want to have their name linked to this.”
Another part of the car still to be proved is the integration of the V8 engine, fuel pump (which is a new model, with much improved efficiency compared with the first unit) and the hybrid rocket system that will provide the final thrust for the car to go through the record barrier. The pump has been fully tested with water, which has very similar physical properties to the high-test peroxide it will pump in the desert, and the rockets themselves have been tested by their manufacturer, Norwegian firm Nammo, but the whole system has yet to be fired. “We’ll take the engine and pump out to Norway in the next couple of months,” said systems engineer Joe Holdsworth. “They have a much better testing set-up there.”
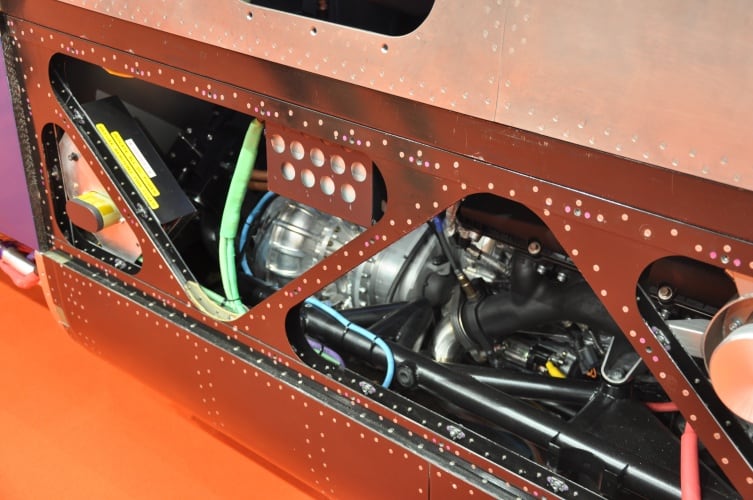
Bloodhound’s next outing will be for runway testing at the team’s operations base in Newquay. It will run on rubber-tyred wheels rather than the solid aluminium discs it will use on its record runs, and will only run at about 200mph under jet power; the main reason for these runs is to shake-down all the electronics and ancilliary systems before heading off to South Africa. “If we have the winglets on we’ll test them, but really we’ll be going too slowly for them to have much effect,” Holdsworth said. “And the same with the airbrakes; we can stop on parachutes and wheel-brakes at that speed, but it makes sense just to test the systems.” Integrating all the systems on the car has been a challenge, Holdsworth explained, particularly because the jet engine, via a gearbox, also runs the car’s electrical generator and hydraulic systems. “Everything for the jet came from Rolls-Royce,’ he explained, “but the gearbox came from another supplier, so we had to make sure it all worked together.”
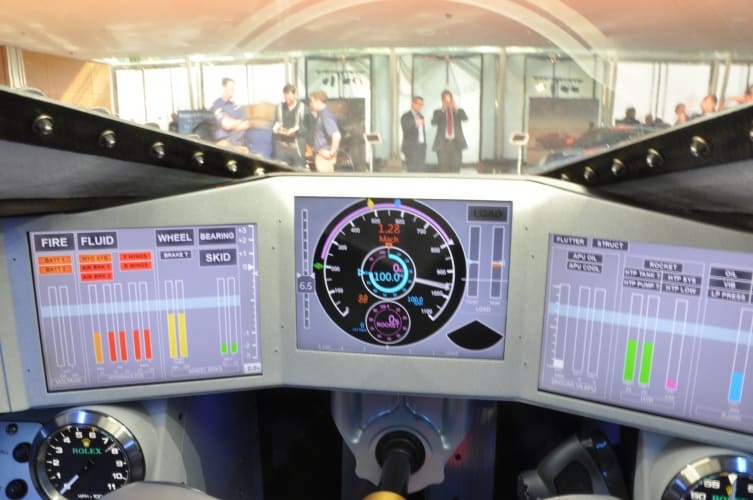
The runway tests will take place “before Easter,” according to Chapman, and the date for the team’s first record attempt has now been announced: 15 October 2016, 19 years to the day after Green first broke the record. Notably missing from the observers will be many of the Army personnel who have worked on the project: most are now back on active service and gathering them from all over the world would be impractical. But for Corporal Holly Jenkins of the REME, who has wired up the cockpit instruments and lighting system, witnessing the public seeing the car and knowing her work is instrumental to the project is reward enough. “It’s definitely something to tell the grandchildren.”
Water Sector Talent Exodus Could Cripple The Sector
Maybe if things are essential for the running of a country and we want to pay a fair price we should be running these utilities on a not for profit...