Bumper model improves testing
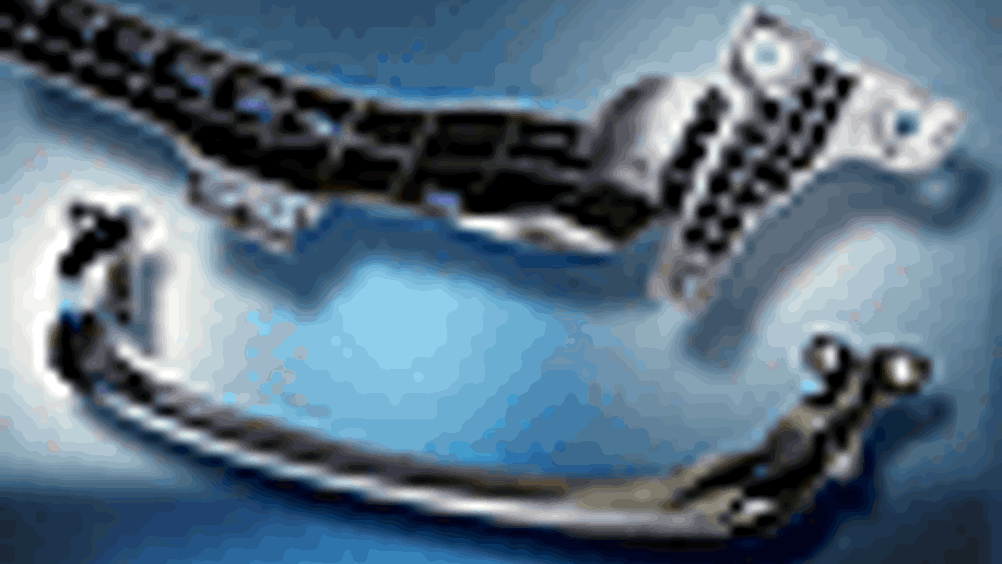
Opel and BASF have used a new mathematical model to create a plastic car part which will reduce the risk of injury during collision with a pedestrian.
The lower bumper stiffener (LBS) is made of BASF’s Ultramid B3WG6 CR, a reinforced polyamide 6 developed for crash applications. The LBS weighs about one kilogram, is one metre long and is installed behind the front bumper so as to reduce the risk of serious knee injury in the event of a collision with a pedestrian.
BASF used a new method of integrative simulation to develop LBS. The numerical material model takes into consideration the directionally dependent behaviour of glass fibre-reinforced thermoplastics. Along with the material parameters of the pure plastic, the content, geometry and orientation and distribution density of the fibres in the finished part all form part of the calculation.
The simulation is fed with the findings from a classic mould-fill simulation and the experimental data obtained from a high-speed measuring device made by BASF. This gives the part shape that best complies with the requirements as well as the optimum mould design.
Register now to continue reading
Thanks for visiting The Engineer. You’ve now reached your monthly limit of news stories. Register for free to unlock unlimited access to all of our news coverage, as well as premium content including opinion, in-depth features and special reports.
Benefits of registering
-
In-depth insights and coverage of key emerging trends
-
Unrestricted access to special reports throughout the year
-
Daily technology news delivered straight to your inbox
Water Sector Talent Exodus Could Cripple The Sector
Well let´s do a little experiment. My last (10.4.25) half-yearly water/waste water bill from Severn Trent was £98.29. How much does not-for-profit Dŵr...