In this introduction to The Engineer's Roundtable on the future of digital manufacturing, Dave Short, BAE Systems's technology director, says that with continued investment and collaborative partnerships manufacturing in the UK should maintain its competitive edge and weather the storms ahead
In an ever-changing political climate it seems to me that the only certainty about the future prospects for the UK’s economy and industrial base is that there really are no certainties. What I am certain of, however, is that our manufacturing sector is well-positioned and ready to collaborate and take advantage of the potential that change offers.
In the past two decades, UK industry and much of our manufacturing sector has benefited from its own investments and deployment of high-end technology, as well as from collaborations with other organisations and government-sponsored programmes, such as the High Value Manufacturing Catapults and the Sector Deals created by the Industrial Strategy. As a result, the UK has been able to maintain its position and deliver some of the most advanced vehicles, aircraft, instruments, high-quality clothing and components that are the envy of the world. “Made in Britain” is still a prestigious tag and proof of a very well-made product. The importance of British manufacturing to our economy is clear from the statistics – with 45 per cent of our exports derived from the sector*.
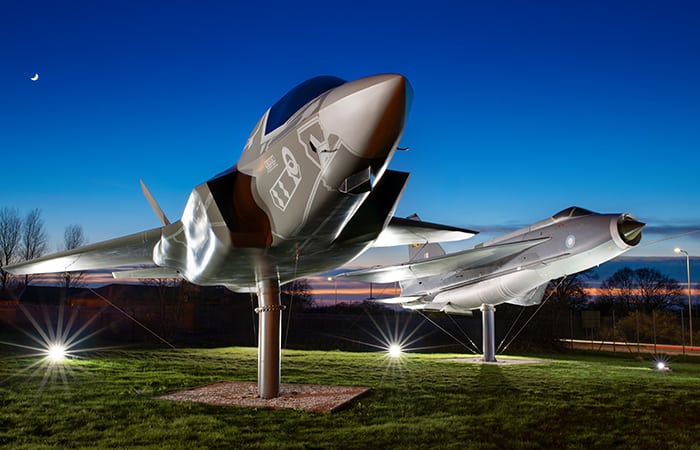
Having worked in the military aircraft sector for more than 30 years, I have seen at first hand the enormity of the industrial ecosystem and collaborative effort required to manufacture and export goods. For BAE Systems alone, this means a £4bn annual spend with thousands of UK suppliers, and training 2,000 young people in engineering and manufacturing environments. The extent of the economic benefits cannot be underestimated, with BAE Systems making an annual £11bn contribution to UK GDP and delivering a multiplier effect of 3.8 jobs in the UK for every job at the company. To put some further context to this, by 2013 the Hawk programme through worldwide exports, had generated a return of £11.5bn for the UK from an initial government investment of £900m.
None of this is achieved in isolation – the collaborative effort with our supply chain is absolutely the key. But constant change and improvement through technological advancement is the order of the day here, as all customers, whether in the commercial or military sector, require higher-performing and more cost-effective and efficient products. In the past decade, I have seen industry and academia alike truly embracing the concept of “open innovation” and technology – in part, driven by more limited resources, but also as a result of the extraordinary pace of technological development underpinned by internet communications and the need to maintain a competitive edge and encourage investment. Gone are the days of “pure research” by universities and this has been replaced by a desire to collaborate and exploit technologies for mutual gain.
I see many examples of this in the manufacturing sector – not least the partnerships between BAE Systems, SMEs and universities to embrace and deploy digital manufacturing techniques to create the factories of the future. Other significant partnerships for us include work with a number of strategically important universities for our business – this includes a project with Cranfield University to develop additive layer manufacturing on a large scale and projects with Manchester University and the Advanced Manufacturing Centre in Sheffield to investigate cobotics and how humans and machines can work together seamlessly in military aircraft manufacture. Increasingly, we are embracing the use of virtual reality techniques to assess spatial clearances, for example in the manufacture of warships and submarines. With expert SMEs we are also exploring advanced layer manufacturing in our maritime and munitions businesses, as well as investigating how acoustic mixing and ultrasound imaging can support our manufacturing processes.
Clearly, continued investment in skills must be an important part of this picture, particularly as the types of roles in manufacturing will change and we will need to train and re-skill people. Traditionally, apprenticeships have been a natural feed for manufacturing roles and here the renewed interest and collaborative work by government, industry and education to change the perception of apprenticeships is welcomed, as is the desire to apply standards across apprenticeships as a measure of quality. Indeed, 86 per cent of manufacturers say they have a responsibility to get involved in schools and training to shape the future workforce, and 71 per cent believe apprenticeships are developing into a proper alternative to higher education for school leavers*.
At BAE Systems, we have always found that employee involvement and empowerment is critical, not just to the adoption of new manufacturing techniques but also to productivity levels. Deploying employees’ ideas for change and improving production is not only motivating for workers but results in working environments that are more productive. We are sharing our experience of this with other companies through a programme called Productivity Through People, which is delivered by the government and industry-sponsored organisation Be the Business, together with the universities of Lancaster, Aston, Bath and Strathclyde – with the University of Swansea soon to join the fold. The programme has been designed specifically for senior managers in SMEs and focuses on developing leaders, nurturing talent and empowering employees. Some 2,000 SME business leaders have signed up to take part in 2019. In addition, BAE Systems’ senior managers are directly mentoring 200 leaders in SMEs as part of the accompanying Mentoring for Growth programme.
To conclude, in spite of huge political uncertainty, I believe that the UK manufacturing sector is in good shape to weather what storms may come. More than ever before, manufacturers are motivated to embrace technology and invest in skills for the future. The resilience and willingness of the sector to collaborate and share best practice can only be to our nation’s long-term advantage.
*figures from The Annual Manufacturing Report 2018
Water Sector Talent Exodus Could Cripple The Sector
Well let´s do a little experiment. My last (10.4.25) half-yearly water/waste water bill from Severn Trent was £98.29. How much does not-for-profit Dŵr...