At a time when inflation is rising and supply shortages are impacting productivity, cost control has never been more important. So, how can manufacturers go about optimising costs when operating in uncertain markets?
Recent months have brought some encouraging signs for the manufacturing industry, with levels of demand for products and services on the rise, and economic recovery also gathering pace. However, at this critical time, a number of factors are making it challenging for manufacturers to manage supply and demand, which could prove an obstacle as they navigate the road to recovery.
Inflation and significant spikes in commodity and energy prices are cause for concern for many businesses. For example, with the supply of petrochemicals still playing catch-up, the cost of plastics is around double what it was 12 months ago. Shortages of HGV drivers and a lack of warehouse space has also led to soaring shipping costs, from £2,500 to £15,000 per container over the last 12 months.
CLICK FOR MORE FROM POLICY & BUSINESS
Other challenges include the knock-on impacts of Brexit, which has led to higher supply chain costs, longer lead times for key components and an increased administrative burden for businesses trading overseas. This is in addition to pandemic-related pressures, such as the need to adapt to social distancing rules, labour shortages and supply chain disruption. For example, as a result of the semiconductor shortage, some carmakers now have a 9-12-month lead time for new vehicles.
Covid-19 has also accelerated changes in consumer behaviour and demand levels; as well as the rise of the e-commerce trend during the pandemic, government-led financial incentives, including furlough, have boosted households’ spending power. As a result, the demand for some products and services has soared to levels previously unseen before the pandemic and for others, has dropped like a stone.
To improve their ability to manage supply and demand over the long term, manufacturers should consider investing in smart procurement systems, enabling them to control their cost base more effectively and buy exactly what they need, when they need it.
Access to real-time dynamic customer and ordering data can also prove invaluable, helping manufacturers to get their supply chain strategy right while delivering exceptional customer service. This should involve capturing and collating critical procurement data and creating bespoke algorithms to inform sourcing decisions.
It’s also essential that manufacturers improve their ability to rapidly respond to changes in market demand by building agility and flexibility into the supply chain. This should start by conducting a robust end-to-end supply chain assessment, focusing on supply chain risk, capability and performance. This will enable businesses to identify where they’re already performing well and spot any areas for improvement. Decision makers can also reduce the risk of supply chain disruption by ensuring that multiple sourcing strategies are in place for key components and commodities.
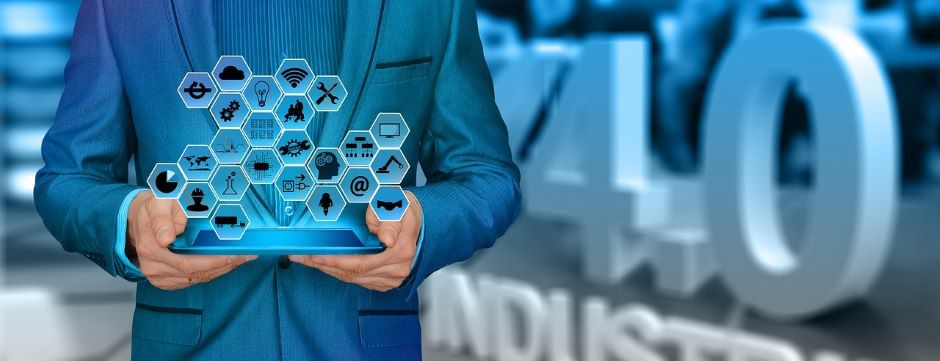
Manufacturing businesses should also make use of tools that allow for sophisticated demand planning and inventory management, combined with a flexible supply chain operating model. Harnessing real-time data from customers and suppliers can help with this, enabling manufacturers to make better informed decisions.
Across supply chains, mounting cost pressures, including the squeezing of margins by lower-cost players, mean manufacturers must look for savings within their supply chain operations, products and services. New business models that include ongoing service and support are also creating a strong incentive for companies to optimise their products’ lifecycle costs.
In order to keep costs under control when balancing supply and demand, businesses need to balance the prices of procurement, manufacturing and assembly, and in-service support. Applying cost and value engineering techniques to products and services in a systematic and integrated way can allow businesses to realise cost savings rapidly, while making cost engineering an integral and sustainable part of their business.
To prevent inflation from eroding their margins, businesses also need to think carefully about whether to pass additional costs onto customers or reduce their cost base to offset the financial impact. Some manufacturers might choose to increase their inventory to get ahead of the inflationary curve. However, it’s important to bear in mind that this could create a cashflow risk and potentially leave them with surplus supplies. Others might find there is scope to share the impact of cost increases with partners in the supply chain.
By looking for opportunities to realise cost savings, making use of real-time data from customers and suppliers and thoroughly assessing their supply chain, manufacturers can better manage levels of supply and demand in an uncertain business landscape.
Paul Cooper is a director at management consultancy, Vendigital
Water Sector Talent Exodus Could Cripple The Sector
Well let´s do a little experiment. My last (10.4.25) half-yearly water/waste water bill from Severn Trent was £98.29. How much does not-for-profit Dŵr...