Competitive coating
A new insulating coating for dies has been developed that can last up to 10 times longer than traditional coatings.
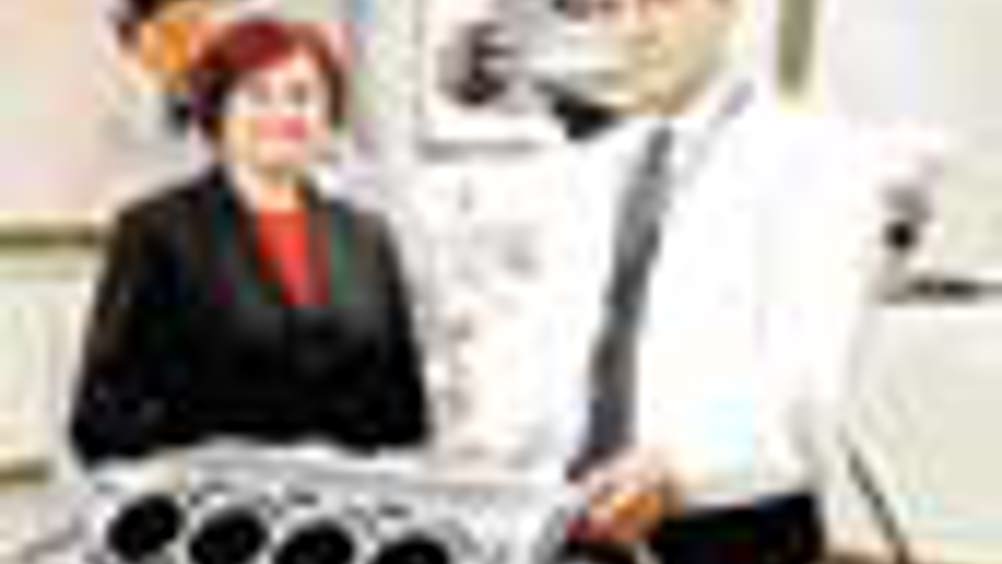
Through work to develop a long-life die coat for the low-pressure and gravity die casting industry, a new insulating coating has been developed that can last up to 10 times longer than traditional coatings.
CASTcoat, as it is called, is a low maintenance coating with adaptable insulating properties. The coating – essentially a strong, porous ceramic layer that is resistant to wear and tear – is applied to a die using a thermal spraying technique.
CSIRO scientists Dr. Mahnaz Jahedi and Stefan Gulizia, and a
In conventional low pressure and gravity die casting processes, filling the die cavity is slow and the metal die has the capacity to rapidly extract heat from the molten alloy. Traditionally, die coats act as insulators to prevent premature solidification of the casting, but they also control the quality of the end product.
Register now to continue reading
Thanks for visiting The Engineer. You’ve now reached your monthly limit of news stories. Register for free to unlock unlimited access to all of our news coverage, as well as premium content including opinion, in-depth features and special reports.
Benefits of registering
-
In-depth insights and coverage of key emerging trends
-
Unrestricted access to special reports throughout the year
-
Daily technology news delivered straight to your inbox
Water Sector Talent Exodus Could Cripple The Sector
Well let´s do a little experiment. My last (10.4.25) half-yearly water/waste water bill from Severn Trent was £98.29. How much does not-for-profit Dŵr...