Composite design shows bruise damage
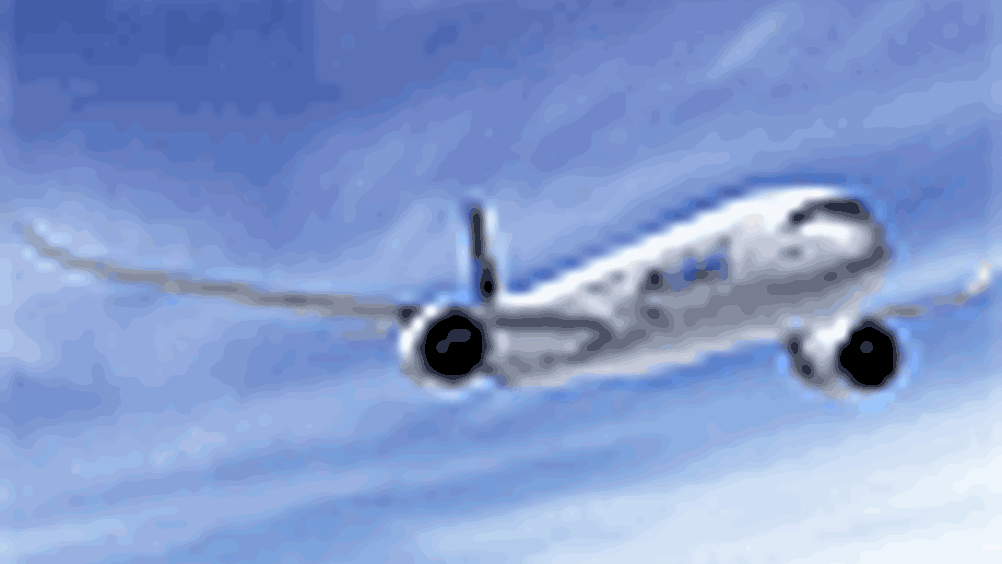
Composite materials that bruise like a person's skin when damaged will simplify and cut the costs of inspecting and evaluating structures.
So claim the British developers of new 'bruisable' composite materials that are being marketed for uses ranging from passively safe lamp posts to aerospace components.
The composites, developed through a consortium led by EPL Composite Solutions of Loughborough, incorporate dye-filled microcapsules into their resin, gel coat or internal layered structure.
'These microcapsules will break from impact loading or overstress and spill their contents of dye into the composite,' explained Matthew Turner, a senior composites engineer at EPL.
The technology, he added, was inspired by techniques used to make carbonless copy paper.
Turner said the capsules will typically break with energy forces ranging from 10-60 joules. The spilled dye appears like a bruise on the composite's surface and inspectors can determine from the size and intensity of the mark whether the material needs a more detailed inspection, repair or replacement.
EPL is looking to manufacture the composites for use in passively safe lamp posts that crumple when impacted to minimise injuries. Posts made of this material, Turner added, will help local councils determine the health of the structures.
EPL is also looking at commercial applications in the aerospace industry. One aerospace supplier has approached EPL with the idea of using the new composites to help detect damage suffered when components move along production lines.
Turner explained that EPL is also considering developing a new kind of composite for aerospace components that would reveal 'invisible' bruises when damaged. The bruises could be detected by inspectors with special UV light systems.
Production of the lamp posts will start within 18 months, said Turner.
'We need to do more tests to ensure longevity in more detail than we've done so far,' he added. 'Currently we've concentrated on polyester resins with our work on bruisable compounds. We need to do work on other resins like epoxies.'
Members of the consortium include: Scott Bader, Smart Fibres, PERA, Exel and BVT Surface Fleet, BMT and Technical Fibre Products.
Register now to continue reading
Thanks for visiting The Engineer. You’ve now reached your monthly limit of news stories. Register for free to unlock unlimited access to all of our news coverage, as well as premium content including opinion, in-depth features and special reports.
Benefits of registering
-
In-depth insights and coverage of key emerging trends
-
Unrestricted access to special reports throughout the year
-
Daily technology news delivered straight to your inbox
Water Sector Talent Exodus Could Cripple The Sector
Well let´s do a little experiment. My last (10.4.25) half-yearly water/waste water bill from Severn Trent was £98.29. How much does not-for-profit Dŵr...