Classic cars accelerate along the road to sustainability
Chris Pickering speaks to Coryton, a company developing low-carbon combustion fuels for vintage engines.
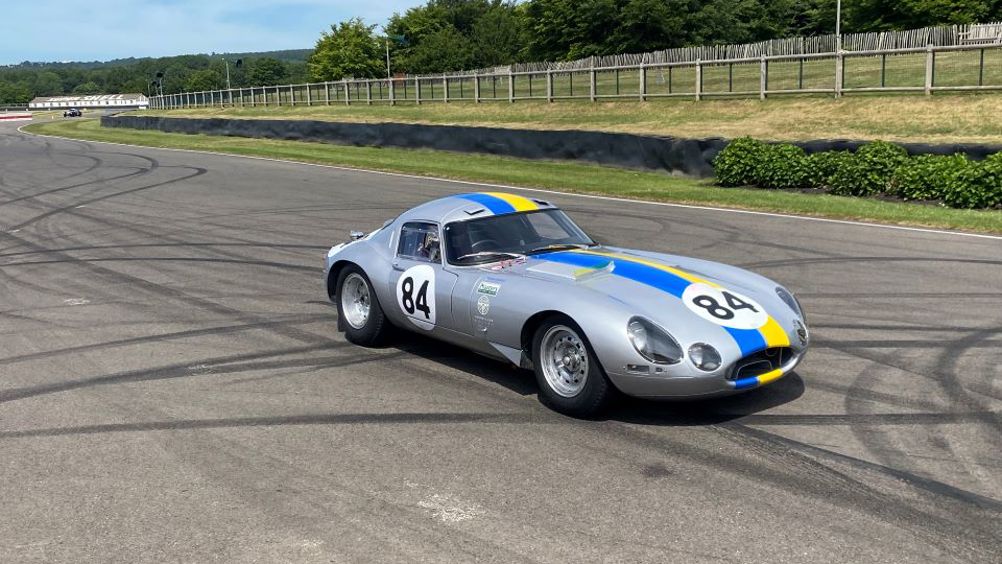
The UK, perhaps more than any other nation, loves old cars. There are upwards of 1.5 million historic vehicles registered in this country. And far from being a footnote, they support an industry employing more than 100,000 people and worth an estimated £18.3bn.
The long-term survival of this industry may eventually depend on its ability to decarbonise. While there is no imminent threat whatsoever to the availability of petrol, mainstream mobility is slowly turning its back on fossil fuels, as is public opinion. And even though the environmental impact of classic cars is negligible, there’s a genuine desire among owners to embrace sustainability.
A growing number of companies now offer electric conversions for classic cars, but manufacturing the batteries carries its own environmental penalty, and purists will question whether it still delivers an authentic classic car experience. For the small volumes involved, low carbon fuels may hold a better solution.
Until now, this technology has largely been the preserve of big-budget motorsport teams. Prodrive, for instance, set a record number of stage wins on this year’s Dakar Rally using a sustainable blend from Essex-based Coryton Fuels that cuts CO2 emissions by a full 80 per cent. A similar concept could potentially put classic car emissions on the road to net zero, while also addressing some of the other challenges posed by modern fuels.
Register now to continue reading
Thanks for visiting The Engineer. You’ve now reached your monthly limit of premium content. Register for free to unlock unlimited access to all of our premium content, as well as the latest technology news, industry opinion and special reports.
Benefits of registering
-
In-depth insights and coverage of key emerging trends
-
Unrestricted access to special reports throughout the year
-
Daily technology news delivered straight to your inbox
Water Sector Talent Exodus Could Cripple The Sector
Maybe if things are essential for the running of a country and we want to pay a fair price we should be running these utilities on a not for profit...