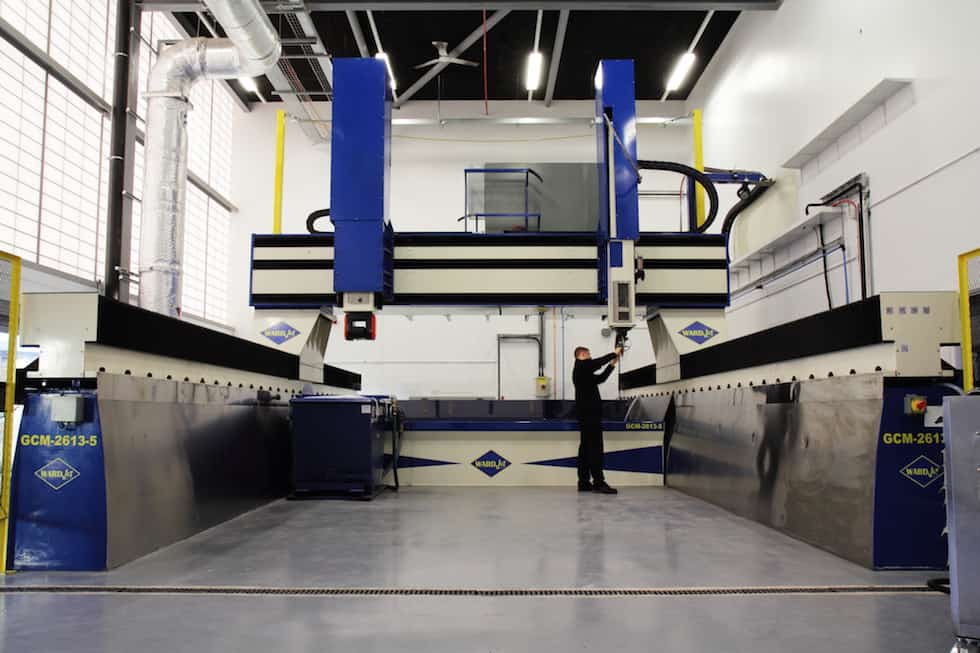
The REFORM project focused on the forming, machining, assembly and recycling of composites.
The University of Sheffield Advanced Manufacturing Research Centre (AMRC) with Boeing coordinated the €7m (£5.5m) four-year project and led research into waterjet cutting and milling of composite components.
Waterjets use high-pressure water containing abrasive particles to erode materials, effectively cutting them.
AMRC designed a new cutting head and a small nozzle to increase accuracy and cutting power. CAM modules were created to optimise cutting and milling parameters.
REFORM coordinator Dr Rosemary Gault, from the AMRC, said: “Manufacturing the new cutting head was really difficult. We did the design quite early on before we figured out how to actually make it.”
“It’s all about the geometry and the assembly, to assemble all the bits together so that it doesn’t all fly apart when the high pressure water goes through it,” she added.
The research resulted in up to 95 per cent recovery of water and abrasives, a reduction of up to 75 per cent in machine and delivery times, and less scrap.
“It’s a lot cheaper because I think they found 60 per cent of the cost of jet cutting is actually abrasive, so you are saving quite a lot of money,” Gault said.
A modular fixturing system was developed to allow only worn sections to be recycled.
“Water jets normally have one big grate and as you are cutting the jet goes through the part and then carries on going through the fixtures, so once you have turned the fixtures around a few times you basically have to take the whole fixture system out and throw it away,” Gault said.
Nine companies from five countries and four research organisations took part in the project, funded by the European 7th Framework Factory of the Future Programme in response to the increasing use of composites in the transport and construction industries.
Work on forming using laser-assisted tape lay-up and augmented reality led to reductions in energy requirements, scrap, time and labour costs.
Research on recycling laminates and fibres produced material using up to 80 per cent less energy at about a fifth of the cost of virgin fibre.
Poll: Should the UK’s railways be renationalised?
I think that a network inclusive of the vehicles on it would make sense. However it remains to be seen if there is any plan for it to be for the...