Greyscale adjustments optimise 3D printed parts
A new additive manufacturing process is being enhanced to bring added light weighting and strength to 3D parts used in sectors including automotive and aerospace.
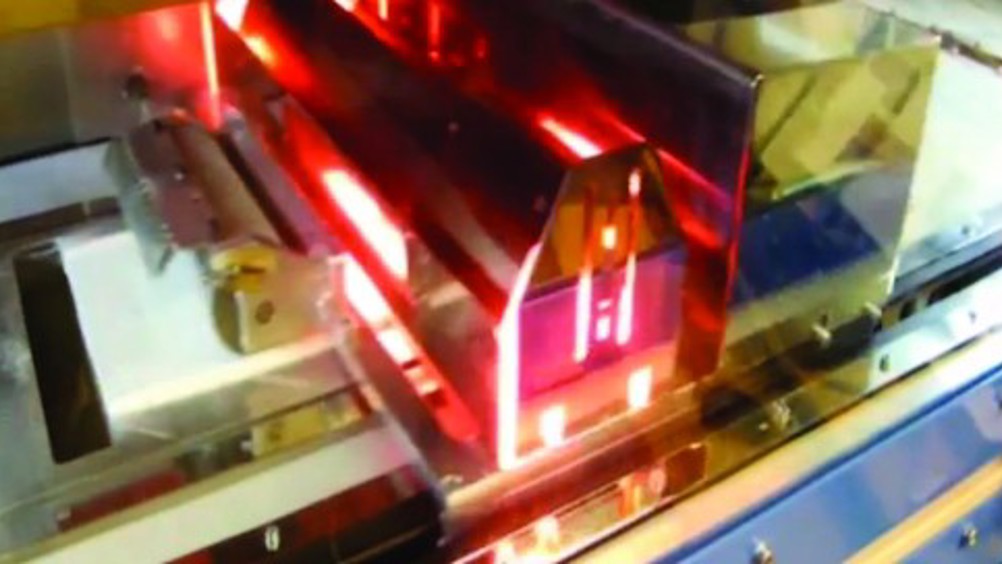
Dubbed high speed sintering (HSS), the process has the potential to produce parts at a rate that could challenge a substantial portion of the injection moulding market.
HSS uses an inkjet and infrared lamps instead of a laser and an advanced optics system to help form 3D printed parts.
‘Its like other 3D printing approaches whereby where we design a part and slice it into lots of discrete layers,’ explained HSS pioneer Neil Hopkinson, a Professor of Manufacturing Engineering at Sheffield University.
Each layer of the 3D CAD design is then uploaded onto an HSS machine, which deposits a layer of engineering grade powder approximately 100 microns thick onto the machine’s part bed.
Hopkinson said: ‘We then print ink onto that powder and that ink is specially designed so that it absorbs infrared energy.
‘We then irradiate the bed surface with IR energy, [which] is particularly suited to be absorbed by the ink that we print but not by the powder that the ink is printed on.
Register now to continue reading
Thanks for visiting The Engineer. You’ve now reached your monthly limit of news stories. Register for free to unlock unlimited access to all of our news coverage, as well as premium content including opinion, in-depth features and special reports.
Benefits of registering
-
In-depth insights and coverage of key emerging trends
-
Unrestricted access to special reports throughout the year
-
Daily technology news delivered straight to your inbox
Water Sector Talent Exodus Could Cripple The Sector
Maybe if things are essential for the running of a country and we want to pay a fair price we should be running these utilities on a not for profit...