Research uncovers alternative fuel source for marine engines
Marine engines may run on hydrogen extracted from seawater thanks to research conducted at Purdue University.
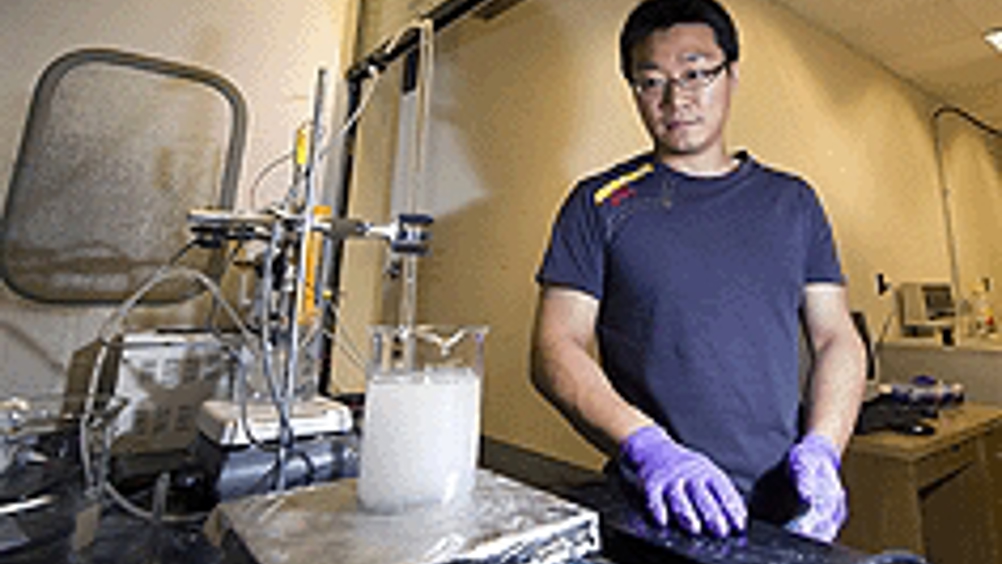
Representing a potential replacement for petrol and diesel fuel in marine applications the method for hydrogen extraction involves using aluminium and a liquid alloy
The technique had previously worked only for freshwater, but a new formulation also enables the method to generate hydrogen from seawater, said Jerry Woodall, a Purdue University distinguished professor of electrical and computer engineering.
Hydrogen generated by the technology could be fed directly to an internal combustion engine.
‘This is important because it might have many marine applications, including cruise ships and tankers,’ said Woodall, who is working with doctoral student Go Choi.
The method makes it unnecessary to store or transport hydrogen - two major challenges in using hydrogen for ships and vehicles, added Woodall.
‘We generate the hydrogen on demand, as you need it,’ said Woodall. ‘It also eliminates the need to store fresh water when used for marine applications.’
Because waste produced in the process could be recycled using wind turbines and solar cells, the technology also represents a new way of storing energy from solar and wind power, he added.
Register now to continue reading
Thanks for visiting The Engineer. You’ve now reached your monthly limit of news stories. Register for free to unlock unlimited access to all of our news coverage, as well as premium content including opinion, in-depth features and special reports.
Benefits of registering
-
In-depth insights and coverage of key emerging trends
-
Unrestricted access to special reports throughout the year
-
Daily technology news delivered straight to your inbox
Water Sector Talent Exodus Could Cripple The Sector
Maybe if things are essential for the running of a country and we want to pay a fair price we should be running these utilities on a not for profit...