Suck it and see
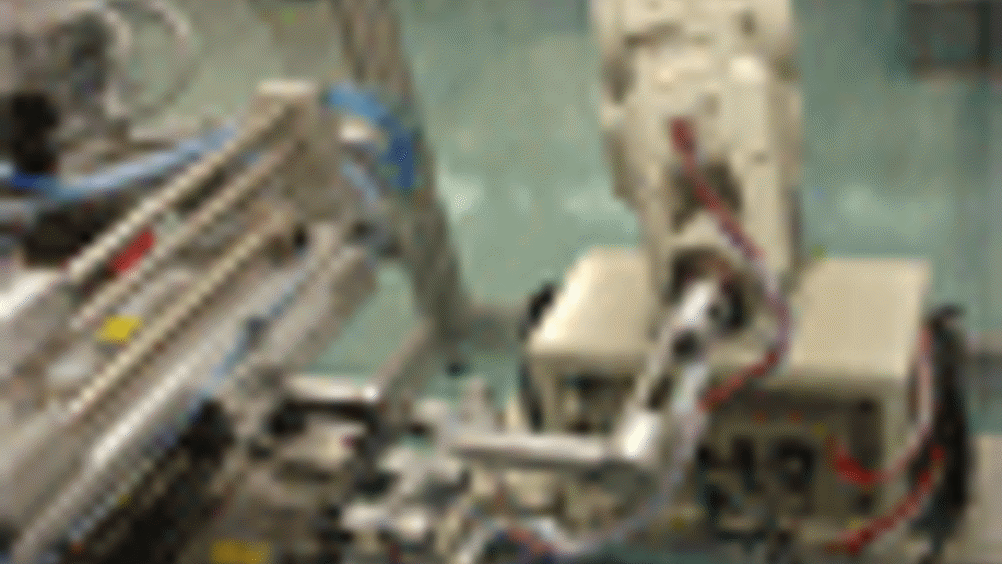
Pennine Healthcare has used a range of Mitsubishi equipment to automate the sterile bagging of its range of Yankauers – suction devices used by surgeons to remove excess fluid from areas of the body during surgical procedures.
Pennine, based in
A yankauer is essentially a rigid extruded PVC tube, with one end attached to a suction line. The free end is chamfered to avoid sharp edges, has a series of radial holes and is angled for ease of use. Further back along its length, the bore diameter is enlarged (through an air injection during extrusion) and a larger hole is provided to allow suction control during use. As well as surgeons, they are commonly used by dentists and vets.
Register now to continue reading
Thanks for visiting The Engineer. You’ve now reached your monthly limit of news stories. Register for free to unlock unlimited access to all of our news coverage, as well as premium content including opinion, in-depth features and special reports.
Benefits of registering
-
In-depth insights and coverage of key emerging trends
-
Unrestricted access to special reports throughout the year
-
Daily technology news delivered straight to your inbox
UK Automotive Feeling The Pinch Of Skills Shortage
Not so much attracting skills to the UK but generating skills within the UK is what is needed! That statement suggest they are in effect wanting to...