Toast and honey holds the key to spider-silk strength
Montreal team exploits complex behaviour of viscous liquids to copy the sacrificial-coil structure that gives spider-silk its strength
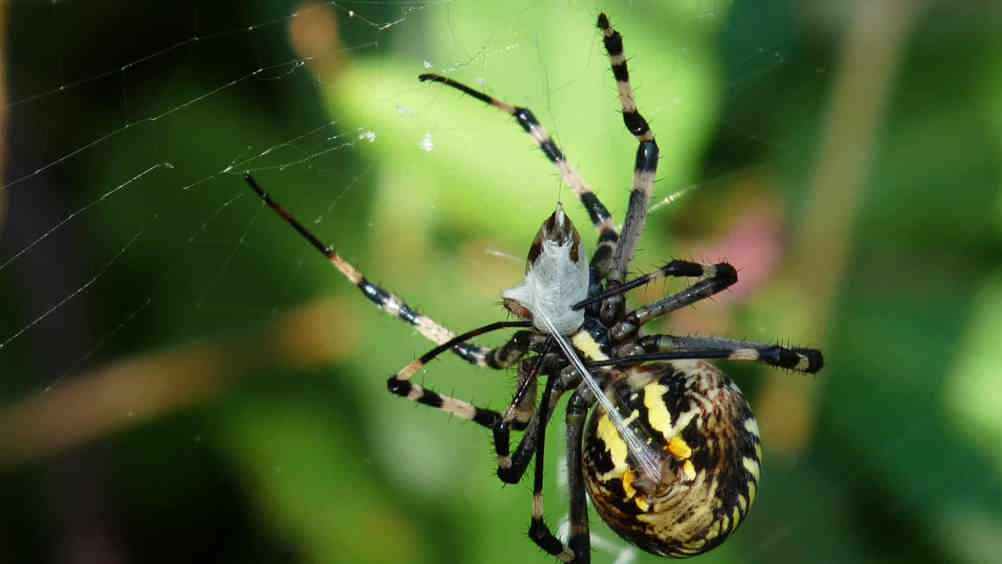
Mimicking the properties of spider-silk has long been a goal of materials scientists. Exceptionally lightweight yet ten times stronger than steel, materials with spider-silk properties would have applications in bullet-proof materials with better characteristic than Kevlar and tyres that could resist highly abrasive and aggressive surfaces.
A team at Polytechnique Montreal is now claiming to have found a way to mimic spider-silk’s strength. “The silk protein coils upon itself like a spring. Each loop of the spring is attached to its neighbours with sacrificial bonds, chemical connections that break before the main molecular structural chain tears,” explained Prof Frederick Gosselin, who is supervising research by Renaud Passieux into the problem. “To break the protein by stretching it, you need to uncoil the spring and break each of the sacrificial bonds one by one, which takes a lot of energy. This is the mechanism we’re seeking to reproduce in laboratory.”
Register now to continue reading
Thanks for visiting The Engineer. You’ve now reached your monthly limit of news stories. Register for free to unlock unlimited access to all of our news coverage, as well as premium content including opinion, in-depth features and special reports.
Benefits of registering
-
In-depth insights and coverage of key emerging trends
-
Unrestricted access to special reports throughout the year
-
Daily technology news delivered straight to your inbox
Breaking the 15MW Barrier with Next-Gen Wind Turbines
Hi Martin, I don´t have any detailed parameters for the 15MW design other than my reading of the comment in the report ´aerodynamic loads at blade-tip...