Tough test
From ship-hoisting in the Gulf to contamination-free medical clean rooms, technology is keeping pace with the increasingly complex demands made of control applications. Julia Pierce reports
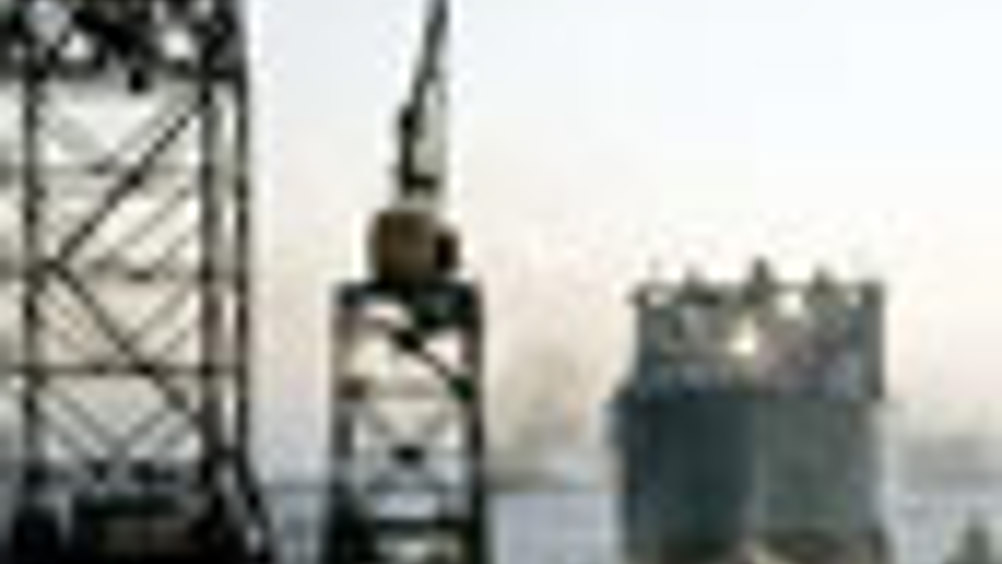
Whether working in construction in the deserts of the Middle East or supporting those searching for oil in the Arctic, wherever hydraulic and pneumatic applications are involved, the technologies are continually expected to deliver more.
Nowadays, such systems are used in highly testing environments, covering everything from the development of landmine clearance equipment to lifeboat launch systems — the RNLI uses systems designed and supported by
of Shropshire.
In the Middle East,
recently successfully supplied the complete drive and control technology for two ship-lifting and transfer installations at purpose-built maritime centre Dubai Maritime City.
These included the use of a powerful wheel tractor with hydrostatic drive to pull ships over a rail transfer system ready to be repaired in the inland dry docks of Jadaf Dubai shipyard, providing the facility with direct access to the sea. The equipment had to be capable of hoisting cargo ships up to 430ft (130m) long and weighing up to 6,000 tonnes out of the Persian Gulf before transporting them overland.
Register now to continue reading
Thanks for visiting The Engineer. You’ve now reached your monthly limit of news stories. Register for free to unlock unlimited access to all of our news coverage, as well as premium content including opinion, in-depth features and special reports.
Benefits of registering
-
In-depth insights and coverage of key emerging trends
-
Unrestricted access to special reports throughout the year
-
Daily technology news delivered straight to your inbox
Water Sector Talent Exodus Could Cripple The Sector
Maybe if things are essential for the running of a country and we want to pay a fair price we should be running these utilities on a not for profit...