Downtime depresses manufacturing
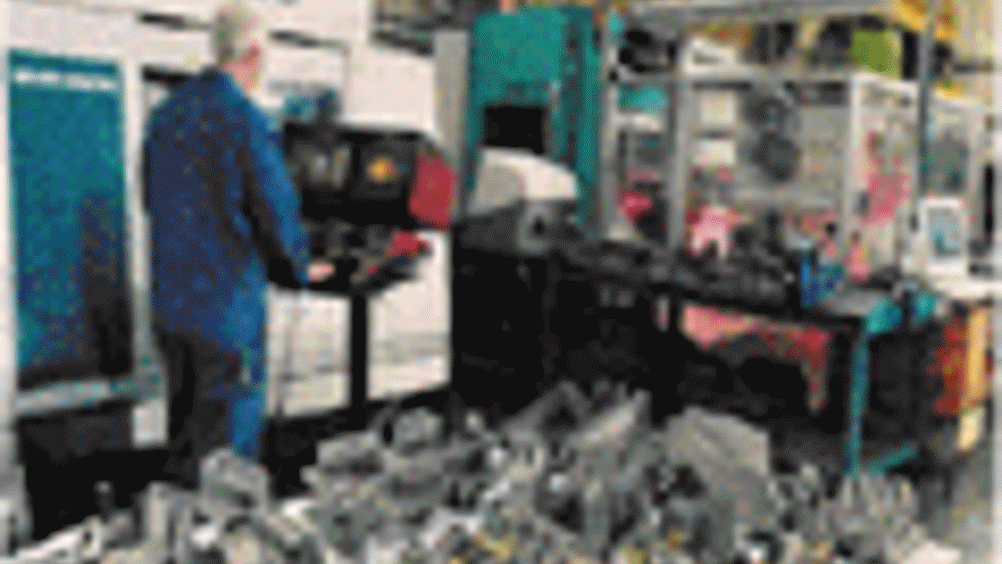
New research suggests that the productivity of UK manufacturing is being held back by the amount of time plant and machinery is out of operation, adversely affecting both profits and morale.
The report, “Downtime: The Problems, Attitudes and Practices in the Manufacturing Industry”, was commissioned by manufacturing efficiency consultancy Idhammar Systems. The aim was to determine the extent to which downtime is a problem for British industry, and therefore a critical strategic business issue, at a time when Government figures show subdued UK manufacturing output. The latest research repeats a similar study commissioned by the company ten years ago.
The study targetting production directors and maintenance managers from 200 manufacturing companies found that most agreed that downtime is a significant problem for their company when vital equipment is not fully functioning, due to repairs, breakdowns, corrective maintenance work or other operational reasons. Downtime nearly always meant lost production time according to 88 per cent of respondents. More than one fifth of the companies believed that product quality was adversely affected, and 41 per cent said downtime was outside acceptable levels.
Register now to continue reading
Thanks for visiting The Engineer. You’ve now reached your monthly limit of premium content. Register for free to unlock unlimited access to all of our premium content, as well as the latest technology news, industry opinion and special reports.
Benefits of registering
-
In-depth insights and coverage of key emerging trends
-
Unrestricted access to special reports throughout the year
-
Daily technology news delivered straight to your inbox
Water Sector Talent Exodus Could Cripple The Sector
Maybe if things are essential for the running of a country and we want to pay a fair price we should be running these utilities on a not for profit...