Energy efficiency without corruption
Engineers can conserve energy by fitting variable speed drives, but the equipment can cause corruption of the mains supply.
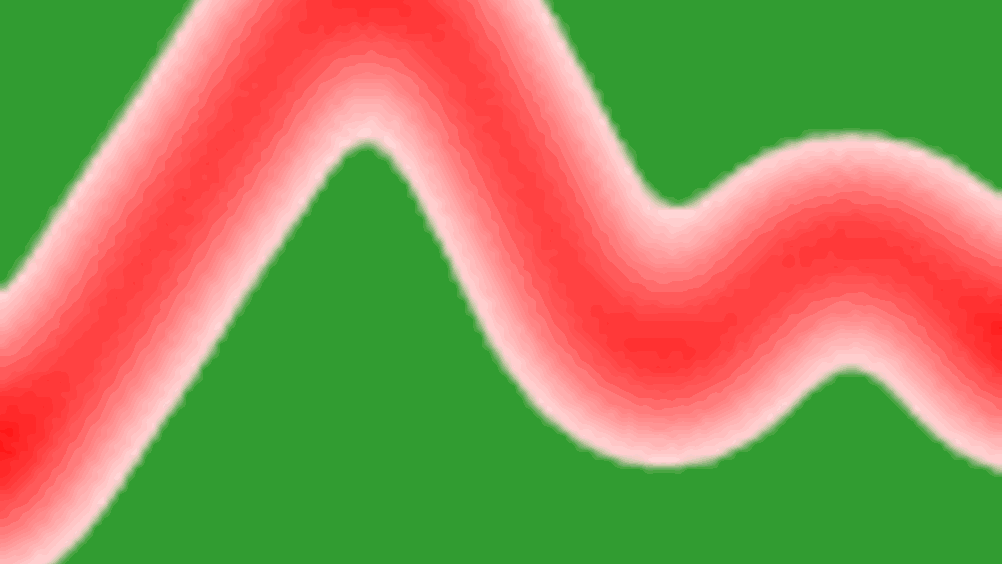
There is ever increasing pressure for plant operators to conserve energy by fitting variable speed drives, but the equipment can cause corruption of the mains supply – against which there is equal official scorn. Until recently, the solution has been seen as fitting a small filter to each drive, but Guy Kennett of Mitsubishi Electric Automation Systems is now tending to favour a single active harmonic filter for the entire plant.
If you want to watch a plant engineer squirm, ask about harmonic corruption. Most engineers have only vague ideas on the subject: they know its important and that it can cause all sorts of problems, but are too busy to get to the bottom of the matter.
The fact that no preferred nomenclature has evolved indicates that the subject has not been widely discussed at a plantfloor user level.
It is generally thought that the following all mean essentially the same thing: harmonic disturbance; mains-borne corruption; dirty power; radio frequency interference, rfi, feedback, noise.
Register now to continue reading
Thanks for visiting The Engineer. You’ve now reached your monthly limit of news stories. Register for free to unlock unlimited access to all of our news coverage, as well as premium content including opinion, in-depth features and special reports.
Benefits of registering
-
In-depth insights and coverage of key emerging trends
-
Unrestricted access to special reports throughout the year
-
Daily technology news delivered straight to your inbox
Water Sector Talent Exodus Could Cripple The Sector
Maybe if things are essential for the running of a country and we want to pay a fair price we should be running these utilities on a not for profit...