Filtering Through Quality
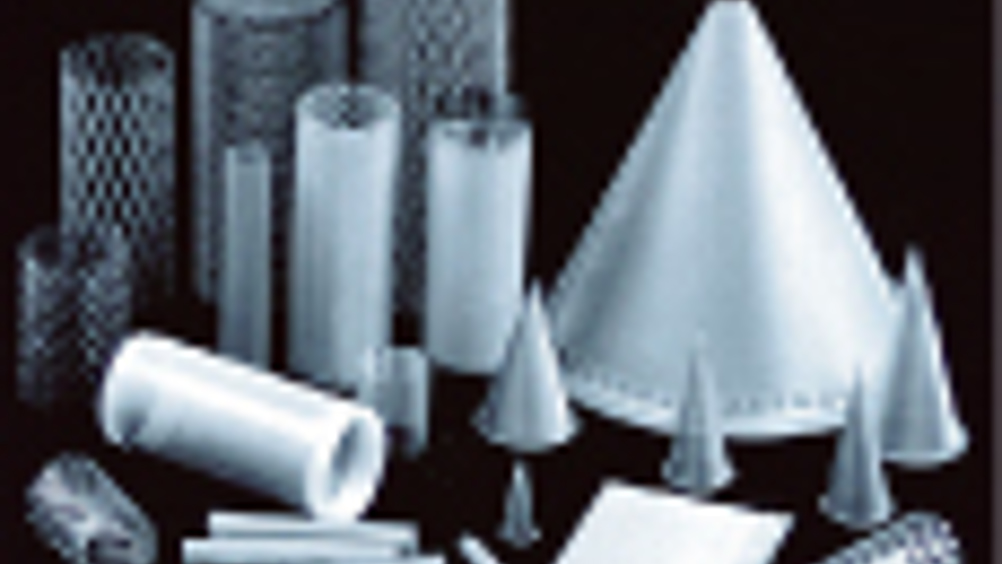
The use of expanded metal mesh is recognised in many industries but the material’s popularity for filtration components is on the increase. Versatile and adaptable, expanded meshes can be pressed, formed, shaped and welded into components for straining, retention and filtration. To cope with the increasing demand in this area, EMC has recently increased its capacity and invested in a new patented mini-mesh machine for finer filtration, further increasing the product range.
“The value of using expanded metal mesh for filtration is both time and cost saving,” comments Deanne Malton of EMC. “Because of its unique formulation, which gives it incredible and unprecedented flexibility and strength significant cost savings can be achieved over comparative perforated or woven materials. It has the ability to be formed into tubes and conical shapes from a range of metals, to meet an extensive range of filtration and retention specifications.”
With the filtration industry recognising the performance capabilities and economic value of expanded mesh, EMC has further extended its manufacturing capacity to include a new range of reinforcement support meshes for pleating, providing optimum strength and flexibility to a multitude of applications. In addition to an extensive range of mini meshes, the company also manufactures a range of aluminium foils.
Register now to continue reading
Thanks for visiting The Engineer. You’ve now reached your monthly limit of news stories. Register for free to unlock unlimited access to all of our news coverage, as well as premium content including opinion, in-depth features and special reports.
Benefits of registering
-
In-depth insights and coverage of key emerging trends
-
Unrestricted access to special reports throughout the year
-
Daily technology news delivered straight to your inbox
Water Sector Talent Exodus Could Cripple The Sector
Maybe if things are essential for the running of a country and we want to pay a fair price we should be running these utilities on a not for profit...