Grain of truth
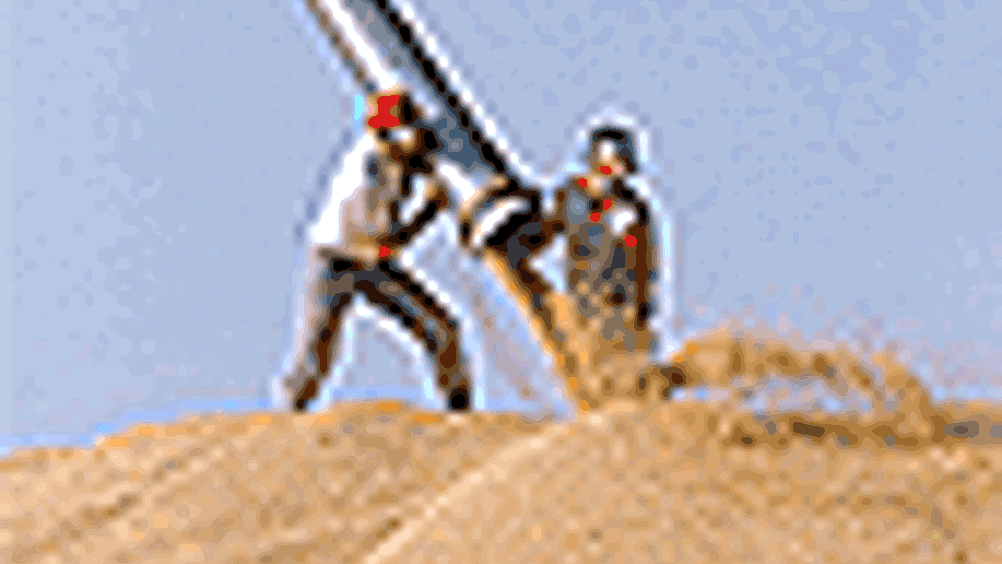
Miniature spies the size of fists that can reveal the state of granular materials stored in industrial hoppers are planned by a group of industry-backed researchers.
The sensor units will interrogate their surroundings then pass the intelligence among themselves and report back to a host computer which will build a 3D picture.
The cereal milling engineering company Satake, of Stockport, and the government's Health & Safety Laboratory, Buxton, are partnering the team from Manchester University, which is building the technology.
The small sensor units will be tossed into the storage containers and wirelessly transmit information about their position and environment. They could trigger alerts when deteriorating conditions threaten to spoil the commodity, whether it is grain, petrochemical products or other loose materials.
'They'll detect things like the temperature, humidity, pressure and the presence of specified chemicals,' said Dr Robin Sloan of the university's electrical and electronic engineering department. 'At the moment this is very difficult to do. Most measurements are taken from the perimeter of the container. Unfortunately this means that their sensitivity is highest at the edges and lowest at the centre. You really want high sensitivity at the centre. We hope our sensors will be able to report accurately from the centre and throughout the material.'
In fact, they should be able to move through the material as it is agitated and reveal its flow. This information could help in the prediction of localised problems, such as hotspots or moisture build-up, and so aid preventative action to stop the material from spoiling.
The technical hurdles are high so the Manchester team is taking it step by step, starting with three- years of EPSRC funding worth £775,000. It expects to produce a demonstrator within that time.
The demonstrator sensor units will measure temperature and surface moisture. Radio communication techniques at microwave frequencies will be used to determine the position of each sensor and transmit data back to the host computer.
The idea is that the sensor units will establish ad hoc networks to forward data between them until it is within range of the host. With enough sensors in a hopper, six or more, the aim is to deduce a near real-time picture of the environment from the collective data.
The team aims to 'develop a demonstrator for on-site mapping of flow patterns within storage hoppers. This is well-suited to address many of the generic long-term wireless sensor network (WSN) research challenges while also delivering a specific diagnostic tool for flow monitoring, safety investigation and process plant design in a relatively short time-scale,' said team member Prof Trevor York.
The design criteria are challenging. The sensors will have to be sufficiently robust to survive in the material unharmed for many weeks. They must have access to sufficient power to gather data and to transmit it. They must not contaminate the material and they should be retrievable. 'It's not by any means a dead cert that we can achieve this,' said Sloan.
One problem already identified derives from the nature of cereal and makes it difficult for the sensor units to communicate with one another and with the host computer. 'Grain is quite a lossy environment and it's not so easy trying to shove the microwave signal for the ad hoc network through it,' said Sloan, 'We'll need antennas printed on the outside of each unit.'
It's one thing being able to transmit a signal through a mass of cereal grains but quite another to keep it going for a few weeks. 'We'll look at power harvesting to supply the units,' said Sloan.
By overcoming some of the current limitations on process imaging, the use of wireless sensor networks could fuel opportunities for increased plant agility, and reduced raw materials uptake, energy usage, environmental impact, waste generation and occupational exposure through an improved knowledge of the process.
'We're taking our cue from industry for this project,' said Sloan. 'When we let it know what we were considering it came straight back and said it wanted it.'
So if there is such a latent demand for a WSN for granular material stores, why hasn't it been done before? 'What we have got at Manchester are six people with the right skills who happen to have been talking at the right time, when the disparate parts of the electronic technologies have matured to a point where it is now feasible.'
Register now to continue reading
Thanks for visiting The Engineer. You’ve now reached your monthly limit of news stories. Register for free to unlock unlimited access to all of our news coverage, as well as premium content including opinion, in-depth features and special reports.
Benefits of registering
-
In-depth insights and coverage of key emerging trends
-
Unrestricted access to special reports throughout the year
-
Daily technology news delivered straight to your inbox
Water Sector Talent Exodus Could Cripple The Sector
Maybe if things are essential for the running of a country and we want to pay a fair price we should be running these utilities on a not for profit...