Moving it about
Colin Carter reports on how automated handling systems can read the colours of gaming chips and help bring the news to the breakfast table.
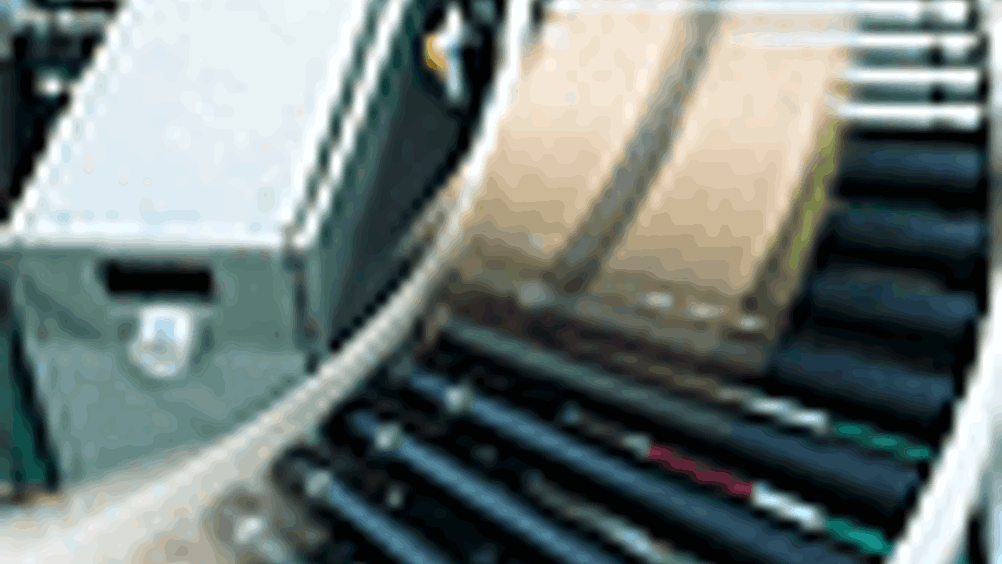
By automating plant or the production of consumer goods it is possible to improve the efficiency with which products are processed or packed ready for transport to the user.
This is not as simple as it sounds. There are many options available to automate basic tasks and position them for the next stage of the process. Add the need for quality control and removing items that do not meet specifications and it becomes more difficult to find the right handling system.
Everyone is familiar with moving conveyors on which items are carried on an (often rubber) belt - you see them at supermarkets and most of us have spent more time watching airport baggage carousels than we would have liked.
There are many types of conveyors in addition to the moving rubber belts we all know. Conveyor systems can also be built using motorised rollers, vibrating beds or even rotating balls (ball transfer units), which can switch the direction of products or pallets and deal with heavy items in multiple units.
Register now to continue reading
Thanks for visiting The Engineer. You’ve now reached your monthly limit of news stories. Register for free to unlock unlimited access to all of our news coverage, as well as premium content including opinion, in-depth features and special reports.
Benefits of registering
-
In-depth insights and coverage of key emerging trends
-
Unrestricted access to special reports throughout the year
-
Daily technology news delivered straight to your inbox
Water Sector Talent Exodus Could Cripple The Sector
Maybe if things are essential for the running of a country and we want to pay a fair price we should be running these utilities on a not for profit...