The accessibility of 3D printing promises to empower both businesses and individuals to create products anywhere. For businesses, the potential to decentralise production and reduce shipping costs is immense. However, it also poses challenges to inventors and designers as the means to make infringing articles on a grand dispersed scale is enormous.

The scale of opportunity for 3D printing in a wide range of fields is only now being discovered: In construction, a Chinese builder recently ‘printed’ ten homes in as many hours, and in Amsterdam, work is underway on the first 3D printed functional pedestrian footbridge. In the field of medicine (‘bioprinting’), surgeons have implanted a 3D printed cranium, as well as vertebrae, and have created a variety of prosthetics including hands, legs, and a nose. The military have used 3D printed parts for RAF Tornado fighter jets, while astronauts have 3D printed replacement parts on demand whilst in orbit. NASA has even successfully tested 3D printed injectors in rocket engines reaching 3,300 °C. Consumer scale applications abound as well, with manufacturers like Adidas and Nike exploring 3D printed footwear, and numerous businesses offering ‘customisable’ 3D printing for certain products. Now with the accessibility of 3D printers growing, so-called ‘maker spaces’ have appeared, not only in repurposed ‘traditional’ copy shops, but also in public libraries. With such innovation, both risks and rewards are changing.
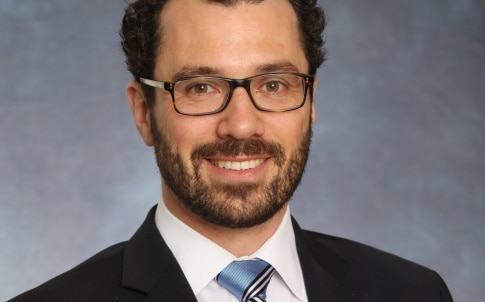
The availability and increasing affordability of 3D printing could lead to an explosion of unauthorised goods being produced and sold. Anyone with access to the appropriate Computer Assisted Design (CAD) files will be positioned to reproduce protected designs without permission of the owner. CAD files may be created by enterprising third parties and made available online to others, either freely or for money. Creating a CAD file can be as easy as scanning a protected design using a smartphone and a freely available app to convert the images into an input file for a 3D printer. With the decentralised manufacturing of illicit goods, identifying and pursuing infringers will be difficult, and costly.
Accordingly, a fresh look at the licensing of patents or design rights is warranted. Traditionally, licenses grant an indemnity to the licensee promising the licensee exclusivity to produce and sell a product, and the licensor must prevent third parties from interfering with such exclusivity. However, imagine granting such an indemnity and then discovering that there are large numbers of small scale infringements via 3D printers; identifying and stopping such infringers could be a considerable headache and be very costly. Moreover, at the smallest scale it may not be an infringement legally, making it impossible to stop, but the indemnity in your licence agreement may still require you to give compensation. So with the increasing access to 3D printing technology, licensors should consider the scope of the indemnity offered to licensees.
3D printing will increasingly allow individuals to reproduce products in their own homes, and as noted above, in many cases this will be done for their own personal use. Reproducing a patented or design protected product, for purely private non-commercial use, will not constitute an infringement of a patent or design. This may not be of significant concern where there are isolated occurrences, but what if many thousands of customers were 3D printing their own personal copy of a patent or design? This would represent a significant loss of revenue.
Manufacturers and rights holders need to be thinking about what the future holds. 3D printing technologically is advancing quickly, and now is the time to work with their relevant trade bodies to consider how to align their business models to the 3D printing opportunities and risks. Identification now of gaps in legal protections, before technology or its use progresses to the point of posing a serious commercial risk, is the best course. There is a clear lesson from the music industry, considering their initial experience with online file sharing. The first response was traditional legal action to stop infringement, but that proved costly and the industry was unable to stop the change in the market. Ultimately, the embracing of paid for downloads and changing the approach to business proved the solution. Will 3D printing require a similar approach from manufacturers? Perhaps we shall see collecting arrangements from websites providing the downloadable 3D printing design files, or with those providing 3D printing services.
New thinking on licences may be the answer. Lower priced non-exclusive licences via the online providers of the designs downloaded to allow printing, may be an option. Though any suggestion of imposing a levy on 3D printers at the point of sale is certain to be met with objections that technological innovation will be stifled, it may still require consideration. Whatever the answer, now is the time to consider new models to protect revenue and maximise future growth in an era of 3D printing.
It is becoming common for consumers to have ready access to 3D printers, whether at home, at a local library, or a 3D printing service. This presents opportunities for new revenue streams by leveraging existing tools; for example the design files that manufacturers already hold and which are used for their existing (and past) product lines. One possibility is to offer customers the option to have their purchases printed at home or at a local service provider, instead of having items shipped. Service providers already exist which support the encrypted transmission of CAD files from the manufacturer to the end user’s 3D printer, where the number of copies of a design have been pre-paid by the customer. Printing items locally benefits both parties by eliminating delivery time, and warehousing and shipping costs.
Another source of revenue may be to re-introduce products which are out of production; the market may be small but value could be there when you take out your production cost. This is evident from the online markets that have already developed which focus on supplying 3D printed parts which are no longer available directly from the manufacturer. Not only does this represent a loss of revenue for the manufacturer, but also a loss of control over the quality of parts being used with their products.
The opportunity is here. Now is the time to re-think licensing, to embrace making available of old product lines, and seize the opportunity of distributed manufacturing. Now is the time to take a lead and be the innovators in a new 3D printing economy.
Water Sector Talent Exodus Could Cripple The Sector
Maybe if things are essential for the running of a country and we want to pay a fair price we should be running these utilities on a not for profit...