Tyred idea bounces back
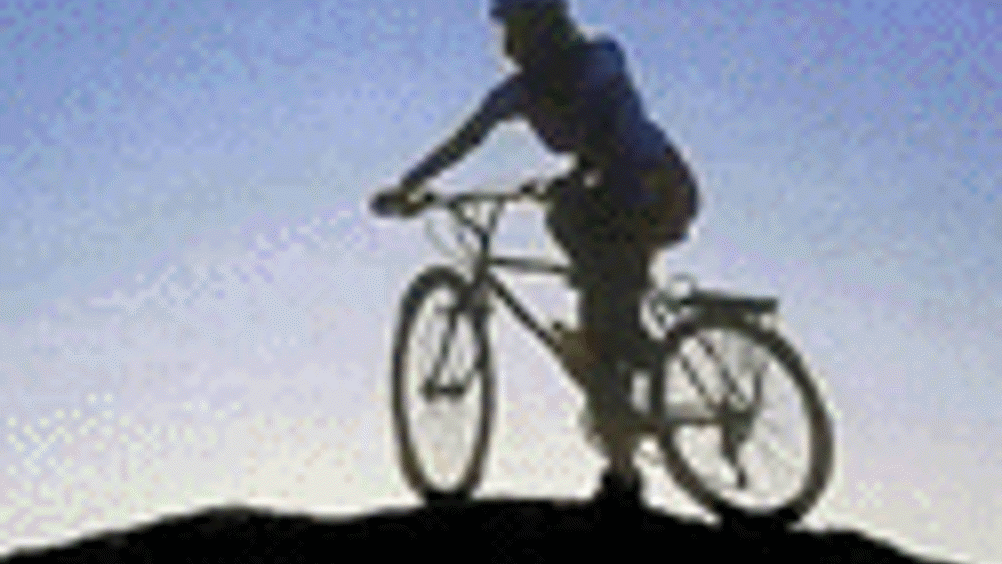
American researchers have found that a footpath surface created from recycled tyres could make cheap and joint-friendly leisure trails for exercisers.
"Some 290 million scrap tyres are generated in the United States annually. That's literally mountains of tyres," said Dr Robert Amme, professor of physics and materials science and manager of the Environmental Materials Laboratory at the University of Denver.
"Our motivation was to find new ways to recycle them. This paving material appears to present a potentially major means of doing that. The process consumes rubber from about 6,000 to 7,000 tyres per mile of trail."
The rubberised surface for footpaths has been developed through extensive laboratory study and multiple field tests using varying compositions. The work was done by Amme, his graduate student Haifeng Ni, and William Meggison.
Their mixture of asphalt, ground-up tyre rubber and a chemical modifier is softer and more resilient for pedestrian traffic than traditional concrete or asphalt, but firm enough for bicycle riding. It's already drawn some commercial interest. The University of Denver has filed for a patent, which is pending.
Register now to continue reading
Thanks for visiting The Engineer. You’ve now reached your monthly limit of news stories. Register for free to unlock unlimited access to all of our news coverage, as well as premium content including opinion, in-depth features and special reports.
Benefits of registering
-
In-depth insights and coverage of key emerging trends
-
Unrestricted access to special reports throughout the year
-
Daily technology news delivered straight to your inbox
Water Sector Talent Exodus Could Cripple The Sector
Maybe if things are essential for the running of a country and we want to pay a fair price we should be running these utilities on a not for profit...