The company may not be a household name, but its products are present in over 37 per cent of the battery electric vehicles (BEVs) for nameplates launched in 2021.
With its HQ in Oxford and corporate offices in Auburn Hills, Michigan, TI Fluid Systems (TIFS) has spent the past 100 years supplying automotive OEMs with advanced fluid handling and thermal management solutions, starting in 1922 with its first contract with Ford Motor Company for unfabricated gas lines on the Model T.
TIFS has since grown into a multinational with 25,600 employees and manufacturing facilities located in 104 locations in 29 countries. Its manufacturing capabilities are located near to – or co-located within – OEM assembly plants, and its Rastatt operations in Baden-Württemberg are no different.
The Baden-Württemberg region of Germany is the country’s automotive heartland and TIFS has set its sights on bringing automotive OEMs to Rastatt to work collaboratively on the thermal management systems that will be vital for the efficient running of BEVs.
There is about double the amount of opportunity for our current fluid handling products in an electrified car than in a combustion engine car
Hans Dieltjens - president and CEO, TIFS
To do this it has opened its first e-Mobility Innovation Centre (e-MIC) in Rastatt with plans to open four more in Michigan, China, Japan and Korea as part of a wider corporate strategy for electric vehicles dubbed Take the Turn (T3). The e-MIC centres will serve as collaborative hubs for OEMs to work with TIFS engineers on developing highly optimised thermal management solutions via the centre’s six core competencies of virtual engineering, design, processing, prototyping, product testing, and vehicle testing.
At an October 2022 press event, Hans Dieltjens, president and CEO of TIFS said: “The Rassatt e-mobility innovation centre was developed with a clear goal in mind: to be a collaborative space for our teams to design, simulate, visualise, prototype, and test the next generation of thermal management systems, modules and components for electric vehicles.”
Rather than threatening the very existence of TIFS, the roll out of BEVs and hybrid-electric vehicles presents a unique commercial opening to a company whose expertise and success has been honed on ICE-driven vehicles for decades.
“There is about double the amount of opportunity for our current fluid handling products in an electrified car than in a combustion engine car,” Dieltjens told The Engineer, adding that the e-MIC is the first of its kind in the world to bring design, prototyping, testing and real-life simulations under one roof.
Every Watt second of energy loss affects BEV driving range and Johannes Helmich, Chief Technology Officer, said that this has led to a reliance on suppliers ‘for the best power fit’.
More from The Engineer
To find the right fit, an OEM’s journey at e-MIC starts with the virtual simulation of a vehicle’s thermal management-based architecture through an interactive 3D simulation.
Developed at TIFS, the 9MP LED screen for 3D simulation measures 9m x by 2.5m and lets engineers display, analyse and redesign 3D models of thermal systems and components within a full electric vehicle architecture in real-time.
The fully interactive nature of the 3D simulator gives OEMs an opportunity, for example, to interrogate a component such as coolant module to see how it would work with different parts.
“Our expectation and our commitment is clearly to come up with a real 3D, simulation,” said Helmich. “I think that’s a real game changer.”
Data from the initial simulation is then translated into product design using software tools like CAD/CAE/CFD and 3D tolerance calculations into a design that meets functional requirements.
Next follows a processing stage where TIFS uses its own patented blow moulding system and a Farsoon Tech HS403 SLS 3D printer to render designs into 3D parts.
Prototyping then gives TIFS’s engineers the opportunity to fine tune parts by focusing on how they will be assembled, and customers are encouraged to witness this stage prior to vehicle validation. Any welds can be carried out on a welding fixation unit that allows for +/- 1mm tolerances and component level checks are done via handheld scanner, with all data recorded for reference. Finished prototypes, which can be RFID-chipped for traceability, are then sent to the customer.
A full range of product tests follows (-40oC to 150oC temperature tests, 3-axis dynamometer tests, plus resonance, fatigue and erosion testing) followed by the integration into the OEM’s BEV for vehicle testing. Data from coolant flow, pressure and NVH (noise, vibration and harshness) is dynamically recorded during driving mode and adjusted to fine tune and maximise the overall performance.
Dieltjens said that taken as a whole, e-MIC can offer up to 15 per cent of energy efficiency improvements, 20 to 30 per cent of weight savings, and deliver 15 to 30 per cent of cost savings.
“We have received a tremendous amount of positive reaction,” he said. “We have received a lot of reactions like ‘you are on the right track, this is really what we want from a supplier for the future.’”
He continued: “We have several programmes that we have been awarded with this technology, but it’s also a rapidly changing world, so we keep innovating and going forward in steps. But it’s getting real, real good momentum in the market.”
Helmich added: “The fact that we are using…simulation tools is allowing us to do changes as they are needed. From our side, we are providing proposals: how you can do it, how you can improve it. That is, I can tell you, what is really appreciated, because of the level of skills we have developed.”
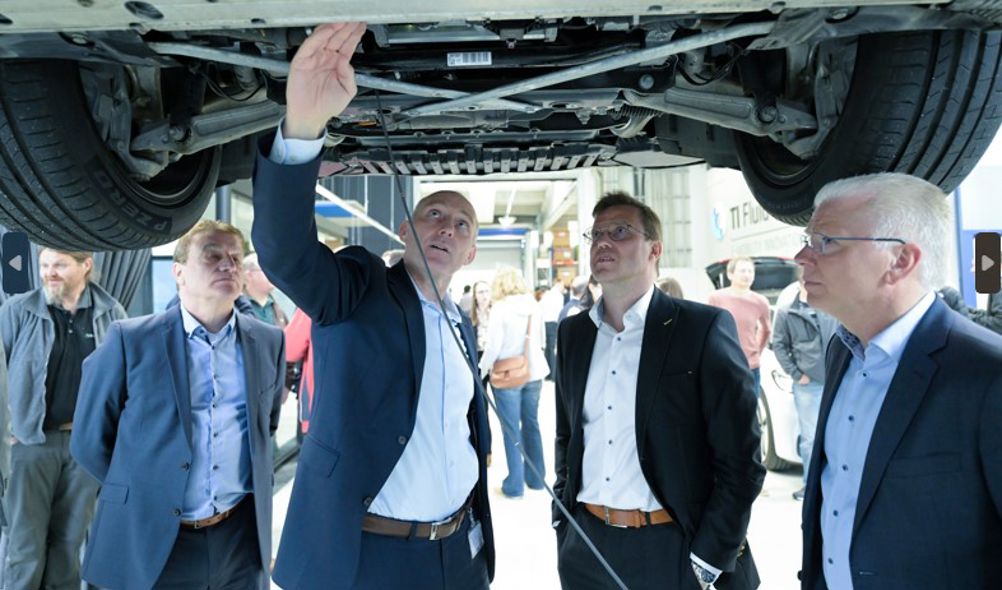
The automotive industry is undergoing a huge shift that requires OEMs to introduce battery electric and hybrid electric alternatives to ICE and TIFS’s T3 strategy has been introduced to help navigate the change. T3 stands for Technology (electrification), Transformation (sustainability) and Talent which, as the name suggests, will see TIFS invest the right staff to fulfill the corporate transition.
For Transformation, Dieltjens said, sustainability will be embedded across the company, from the electricity it uses to the materials used in its products, which Helmich said will be recyclable and CO2 neutral.
“It’s not what we do but how we do it: what path do we walk to get there?” said Dieltjens. “We’re focusing on the sustainability of how we do things through ESG.”
To this end, TIFS has committed to reducing its Scope 1 and 2 CO2(e) emissions by 37.5 per cent by 2039 compared to 2019 emissions levels, aiming for maximum annual emissions of 191,927 tonnes in the agreed timeframe. The journey to emissions reductions aims to see a 16 per cent reduction of Scope 1 and 2 emissions by 2029, and a 26 per cent reduction by 2034 before hitting the 37.5 per cent target in 2039.
“That’s a clear commitment,” said Dieltjens. “We’re doing that in two ways, this is saving energy, buying green, and there is a clear plan we have worked through, a lot of activity going on currently in the company around that, and to identify what is the best opportunity [to] save energy.”
He added: “We’re working with an external partner on that who’s very knowledgeable [about] this, but also on how to acquire and how to buy green energy, which in the first instance seems very straightforward, but it isn’t. It is more complex than you would think.”
Thirty-one EV charging points can be found the Rastatt site, which runs on renewable energy and across the business the company has installed LED lighting, eliminated compressed air leaks, installed balancing heating and cooling systems plus automatic shutoff controls, and is using variable motors wherever possible.
“ESG is a very important part of our business and of how we go forward,” said Dieltjens. “I always say, why would you make green products in a non-green way? That doesn’t make any sense to me.”
Poll: Should the UK’s railways be renationalised?
Correlation does not equal causation! That's a hugely simplified view of things and ignores things like increasing car ownership, increasing commuting...