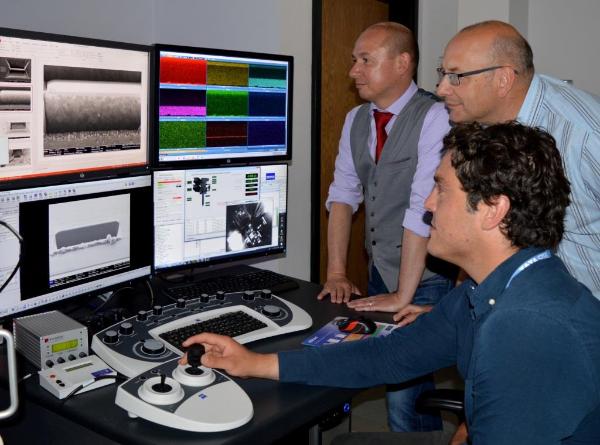
Corrosion inhibitors have a variety of applications and are commonly used to coat and protect steel products. To date, hexavalent chromate has been commonly applied as a common corrosion inhibitor, but will be prohibited in the EU from 2019.
The Swansea team’s breakthrough is applicable to coated steel products, and their efforts have been rewarded with the £25,000 Materials Science Venture Prize from The Worshipful Company of Armourers and Brasiers.
The new innovation contains a stored reservoir of corrosion inhibitor that works by channeling electrolyte anions into the coating, triggering the release of the inhibitor. The product has been tested with salt spray, the standard test for corrosion, outperforming hexavalent chromate.
“We believe we are well ahead of other chrome-free products,” said Dr Adrian Walters, IP & Project Manager, SPECIFIC IKC, an academic and industrial consortium led by Swansea University. “We have tested the leading competing products and none perform nearly as well as our product, which is comparable to chromate in performance and price.”
The £25,000 prize will be used to purchase a Jet Mill system to help eradicate the technical barriers to commercialization.
Walters said: “Commercial grade inhibitors have uniform particle size around 5µm to ensure the material remains homogenously dispersed in the primer system during processing.
“Achieving this fine uniform particle size is technically challenging and to date we have only produced inhibitor with a non-uniform particle size distribution in the range of 10µm to 140µm, unacceptable for commercial processing. A Jet Mill will enable us to overcome this.”
The research was carried out using a scanning Kelvin probe that was built by the Corrosion Group at Swansea University. In use, the instrument detects the state of the metal beneath a coating, which allowed the team to conduct tests in around 24 hours, rather than 500 hours.
Poll: Should the UK’s railways be renationalised?
I've been watching some of the TV interviews with some level of incredulity. I do recall that the last time this was mooted the cost was in the region...