Casting technology
A steel casting technology developed by the US Department of Energy is to be used to manufacture improved armour for vehicles.
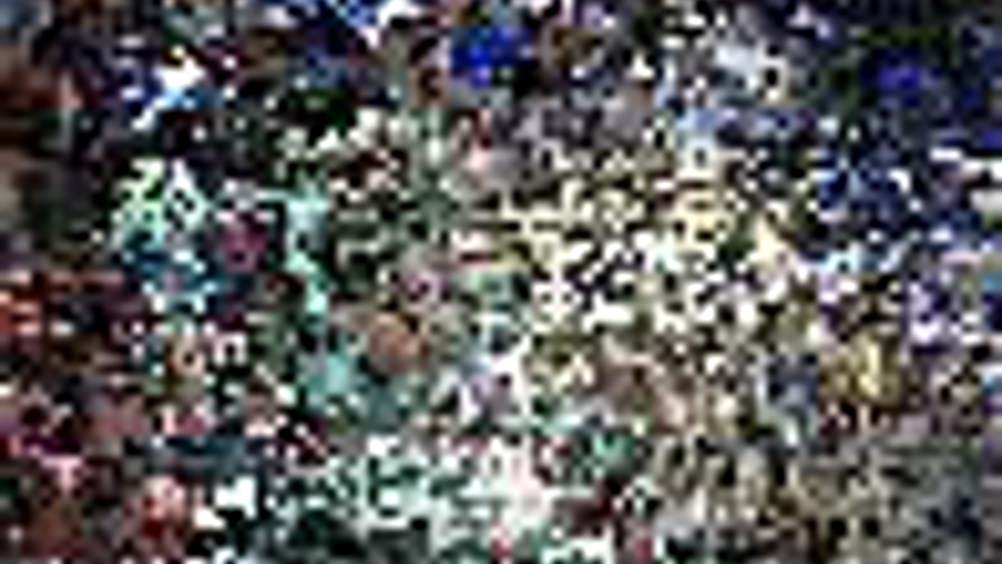
A steel casting technology developed by the US Department of Energy has been transferred to the US Army's Rock Island Arsenal to manufacture improved armour for vehicles.
The Office of Fossil Energy's National Energy Technology Laboratory (NETL) provided the Rock Island Arsenal with process guidelines, parameters, expertise, and patterns to set up and operate a facility for making steel castings using an NETL-developed process called loose-bonded sand, lost-foam technology. The facilities at the arsenal, in Rock Island, IL, will be used to produce the improved cast steel armour plating for Army vehicles.
The Rock Island Arsenal - the western world's largest government-owned weapons manufacturer - produces weapons and weapons components at scales from prototype to full-scale sizes. NETL scientists have designed and produced patterns and gating systems for casting armour plate in the Arsenal's foundry, and they are continuing to assist US Army researchers with process-related information and procedures.
In NETL's loose-bonded sand, lost-foam technology for casting steel, researchers make a foam pattern of a part, then dip the pattern into a water solution containing a suspended refractory. The refractory material coats the foam pattern and leaves a thin, heat-resistant layer. After sand is poured around the pattern to provide support, molten metal poured into the mould melts and vapourises the foam. The solidification of the metal and its removal from the sand gives rise to the name lost-foam casting.
Register now to continue reading
Thanks for visiting The Engineer. You’ve now reached your monthly limit of news stories. Register for free to unlock unlimited access to all of our news coverage, as well as premium content including opinion, in-depth features and special reports.
Benefits of registering
-
In-depth insights and coverage of key emerging trends
-
Unrestricted access to special reports throughout the year
-
Daily technology news delivered straight to your inbox
Water Sector Talent Exodus Could Cripple The Sector
Maybe if things are essential for the running of a country and we want to pay a fair price we should be running these utilities on a not for profit...