Crash helmet
The European project Custom-Fit enables fully personalised consumer goods, such as crash helmets, to be made cost effectively.
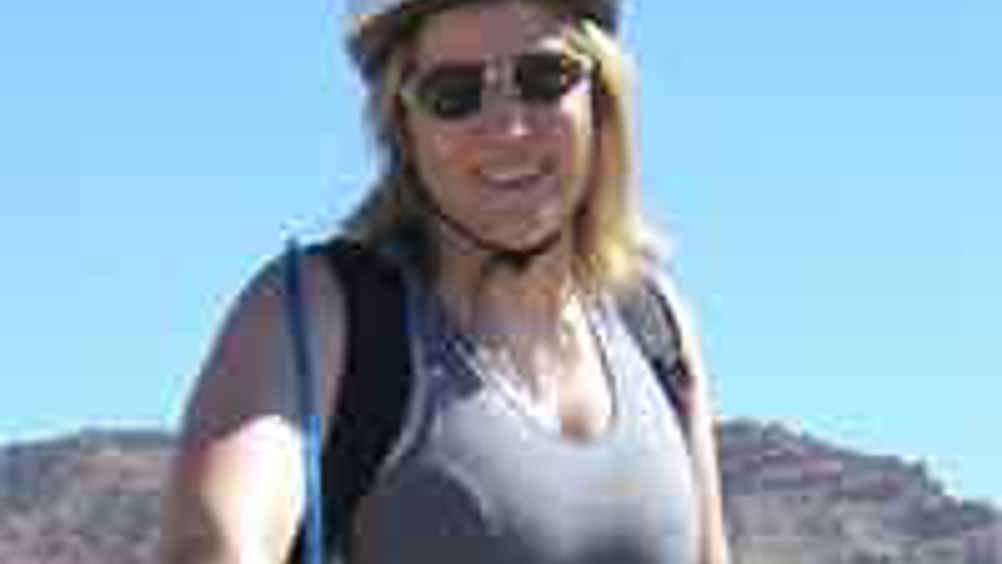
A recent survey revealed that five per cent of motorcyclists have problems in finding a perfect fitting crash helmet. An even higher percentage resign themselves to buy one that is slightly too large or slightly too small.
Mass production cannot solve this issue and only partial personalisation can be done by playing with different padding thicknesses. A new manufacturing philosophy is needed to produce a fully customised helmet, perfectly formed to the geometrical features of individual riders.
Now, the European project Custom-Fit, funded by 6th framework program, offers a solution. It enables fully personalised consumer goods, such as crash helmets, to be made cost effectively.
The Custom-Fit process works by capturing the geometrical characteristics of the consumer’s body using a 3D scanner. Then, specialised CAD software allows individual features to be added. Finally, the customised part is manufactured with additive techniques.
In the case of the helmet, the rider’s head shape is first scanned with a laser scanner developed by one of the Custom-Fit partners Human Solutions. The scanned surface model represents the reference point from where adaptaptations are made on a standard design, resulting in a helmet design perfectly shaped to the rider's head (carried out with a specialised CAD tool from the project partner Delcam).
Register now to continue reading
Thanks for visiting The Engineer. You’ve now reached your monthly limit of news stories. Register for free to unlock unlimited access to all of our news coverage, as well as premium content including opinion, in-depth features and special reports.
Benefits of registering
-
In-depth insights and coverage of key emerging trends
-
Unrestricted access to special reports throughout the year
-
Daily technology news delivered straight to your inbox
CCC Report Finds UK Climate Targets Still Within Reach
In 1990 67% of the UK´s electricity came from coal-fired power stations and even without renewables the transition to gas was a major contributor to...