Sizing up the situation
Mobile wireless mini sensors could save time and money by anticipating possible mechanical faults.
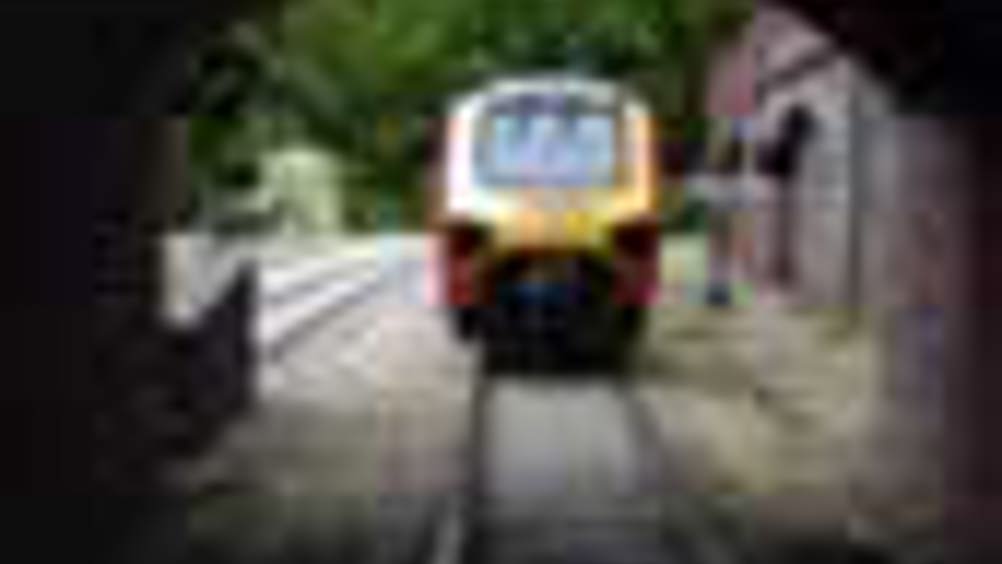
UK researchers are developing wireless miniature sensors which can detect wear and tear in machinery and predict when it might break down, thus reducing maintenance costs for industry and potentially improving safety.
The research — part of Dynamite, a European project involving 17 academic and industrial partners — is being carried out at
.
According to Dr Andrew Starr from the university's school of mechanical, aerospace and civil engineering, the entire project is linked by the concept of 'e-maintenance'. The sensors that his team are developing will form part of a suite of mobile monitoring technology that could be integrated into a variety of applications such as trains and agricultural vehicles, as well as in manufacturing and plant machinery.
One requirement of the sensors is that they must be self-powered. Starr said that this is because in conventional sensors the cable that carries the data also delivers power. 'It is very important that they are self-powered and so we need a clever strategy to generate sufficient power to deliver signals from the sensor — not continuously, but when they are required,' said Starr. Only very small amounts of power are required to run the system as researchers envisage they will only have to give occasional indications that the entire system is healthy rather than continuously stream unnecessary data.
Register now to continue reading
Thanks for visiting The Engineer. You’ve now reached your monthly limit of news stories. Register for free to unlock unlimited access to all of our news coverage, as well as premium content including opinion, in-depth features and special reports.
Benefits of registering
-
In-depth insights and coverage of key emerging trends
-
Unrestricted access to special reports throughout the year
-
Daily technology news delivered straight to your inbox
CCC Report Finds UK Climate Targets Still Within Reach
In 1990 67% of the UK´s electricity came from coal-fired power stations and even without renewables the transition to gas was a major contributor to...