Up in arms
The muscle structure of an elephant's trunk inspired researchers to create a new type of robotic arm, and the technology could have wide uses. Siobhan Wagner reports.
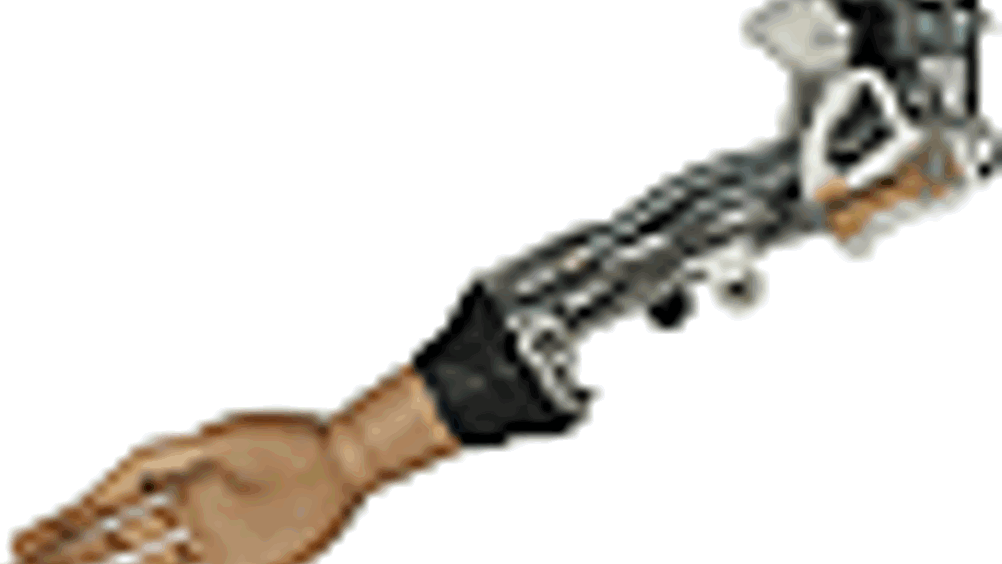
A new robotic arm that draws inspiration from an elephant's trunk is claimed to be less expensive and safer to operate than previous designs. The device, called Isella, uses multiple systems of motors, drive shafts and cords to work like the muscles in a human arm or an elephant's trunk.
The researchers behind the development, from the
(IPA) in Stuttgart, believe the concept could be applied to a variety of devices, such as factory robots or cranes in container seaports.
Harald Staab, the IPA researcher who invented and developed the technology, said his research team had originally used an elephant's trunk as a model because of its strength and agility. A trunk contains about 40,000 muscles, and is used to grasp objects and to drink.
With their trunks, elephants can tear down trees and pull heavy loads but are also capable of performing extremely delicate manipulations.
Staab said he thought such delicacy would be useful for robotic arms, which can pose a risk to human operators if technical glitches cause wild, uncontrolled movements. Staab and his team designed Isella to make such problems less likely by giving the arm 10 muscle-like systems, which he admits is significantly less than the number in an elephant's trunk.
Register now to continue reading
Thanks for visiting The Engineer. You’ve now reached your monthly limit of news stories. Register for free to unlock unlimited access to all of our news coverage, as well as premium content including opinion, in-depth features and special reports.
Benefits of registering
-
In-depth insights and coverage of key emerging trends
-
Unrestricted access to special reports throughout the year
-
Daily technology news delivered straight to your inbox
Pipebots Transforming Water Pipe Leak Detection and Repair
Fantastic application.