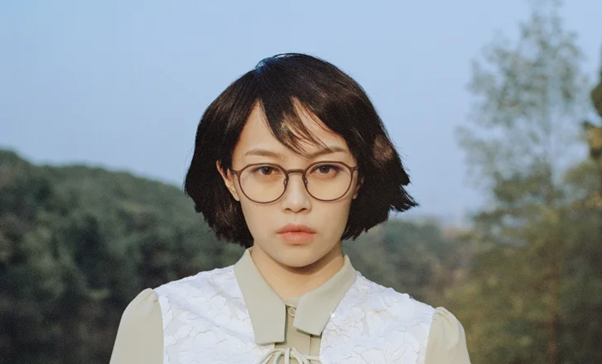
"One size fits all" - a nice idea, but often not feasible. This applies especially to acetate frames manufactured using the traditional injection moulding or 2D cutting process - individual face shapes with their decisive nuances are simply too different. In some cases, the lenses may even be at the wrong distance from the eye, or the wrong height in relation to the pupils.
“We are already familiar with the concept of customised production from numerous other applications, for example in the medical sector,” said Gong Xinyi, designer at BRAGi. “After all, prostheses or implants are also tailored to individual patients. So why wouldn’t the same concept work in the field of optics?”
More from Industrialising Innovation Week
Selective Laser Sintering (SLS) is a proven technology that has been successful and established for many years. A laser prints a part layer by layer - ideal for a high degree of customisation without additional costs. All that is required is an industrial 3D printer and material plus the corresponding 3D computer data. Any component can be easily and quickly produced from the data. This also applies to eyewear, which are delicate but still need to be robust and fit precisely.
The additive solution found by BRAGi takes all this into consideration. Data points from the shape of the head are captured using a 3D scanner. An optician takes several photos of the person’s head with a camera mounted on a tablet, allowing the look of the new glasses can also be checked immediately with a virtual representation. Other designs can also be quickly checked with the subject's own face.
Afterwards, the frame is individually manufactured for its wearer. The frame is always produced in white nylon and given a finish during post-processing with one of 14 different colours. A pure white and easily post-treatable surface is particularly important for high-quality colouring. For additive manufacturing, BRAGi uses FORMIGA P 110 Velocis systems and EOS's proven PA 2200 material.
“We intensively compared the technologies of different suppliers from all over the world,” said Gong.
“The EOS system is superior to other manufacturers in terms of component quality and surface finish. The fit between frame and bracket is excellent for every build cycle, and the technology-related staircase effect is virtually non-existent. In addition, the material allows any form of finish, including colouring. The purity of the white of the glasses frames is also very important, and here again the EOS system is at the top.”
In the space of just a few months, BRAGi has already produced over 30,000 pairs of glasses and shipped them to customers with a short delivery time. The company has expanded its business outside China to activities in Korea, Japan, Indonesia, Singapore, Thailand and Malaysia, and has also received inquiries from Europe. A scan at home is also planned in order to make the process even more convenient for customers.
Poll: Should the UK’s railways be renationalised?
Rail passenger numbers declined from 1.27 million in 1946 to 735,000 in 1994 a fall of 42% over 49 years. In 2019 the last pre-Covid year the number...