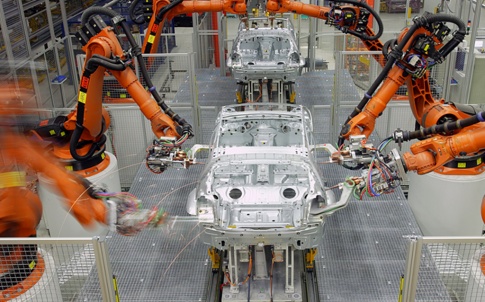
Automotive is a crucial industry in the UK, contributing over £20bn to the country’s economy in 2017 and producing a total of 1.52m passenger cars in 2018. Though the number of UK cars manufactured has declined in recent years, global trends indicate rising demand in regions with growing economies such as India.
Cryogenic storage could enable safe transport of car batteries
C2I 2019: UK developed magnet-free electric motor ready for the road
The move to reduce the carbon footprint of the automotive industry has driven greater innovation in the design and manufacture of vehicles. This includes government legislation to favour hybrid and electric vehicles, as well as generative design to improve the way we make car parts, through lightweighting and less wastage in the manufacturing process.
Global competition between automotive manufacturers incentivises the innovation, and digitisation and automation have emerged as the leading technologies to enable the entire automotive value chain to compete and avoid being left behind.
However, the constant companion to new and emerging technology is apprehension: fear of change and in some cases, fear of getting things wrong. Advanced software, automation and new technologies are perceived as expensive. There’s also a skills gap that needs addressing to manage these new technologies. Within the realm of CAM, design and engineering software, in particular, the question often is: does the technology enable greater efficiencies?
Here are a few ways technologies can overcome key challenges within the automotive supply chain:
Lightweighting through generative design
As global environmental goals get translated into enforceable regulatory frameworks, electrification will give automotive manufacturers a proven way to achieve compliance. Increasingly stringent requirements for greenhouse gas emissions are just one example. Current regulations in Europe allow 130g/km of CO2 emissions but this will drop sharply to 95g/km by 2020, with long-term targets becoming even more aggressive.
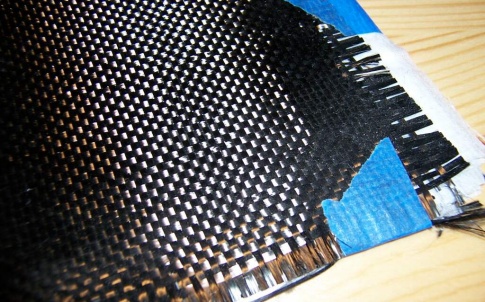
At the same time, consumer demand for vehicles with lower costs of ownership – especially, improved fuel economy – are also accelerating. While there are several different options available to achieve fuel economy targets, automotive lightweighting is emerging as a clear favourite.
Materials are inevitably the first thing considered, when it comes to reducing weight – and improving overall vehicle performance and through-life costs. However, vehicle lightweighting can be better achieved using additive manufacturing techniques – which can help speed up supply chains too.
The process gives vehicle manufacturers a proven way to improve fuel economy by replacing components with a variety of lightweight materials, including aluminium, magnesium, high-strength steel, plastics, and carbon fibre. Reducing the weight of a vehicle even by 10 per cent typically delivers a 6 to 7 per cent increase in overall fuel economy.
Depending on the vehicle, 3D printing can also be used to produce lightweight components, personalised components for mass customisation and on-demand prototypes for generatively designed parts.
The potential for these technologies in automotive manufacturing is already being tested, which can act as a major learning curve for motorsport manufacturers. General Motors (GM) is using generative design to promote lightweighting and simplify supply chains to reduce the cost of making electric and autonomous vehicles. In a recent collaboration with Autodesk, GM engineers designed a new, functionally optimised seat bracket.
This standard auto part, which secures seat-belt fasteners to seats and seats to floors, typically features a boxy design made up of eight separate pieces. Using generative design software, GM came up with more than 150 alternatives that could be manufactured via 3D printing. The finished part is made from a single piece of stainless steel and is 40 per cent lighter and 20 per cent stronger than its predecessor, which consisted of eight pieces welded together.
Visualising the end result to reduce prototyping costs
Another challenge facing manufacturers is ensuring that development costs are kept under control. The automotive industry has traditionally heavily relied on physical prototyping, from early-stage clay or foam models all the way through to disguised but functioning ‘mules’, which is costly and time-consuming.
However, simulation software is a very effective way of cutting time to market, while also keeping costs low. Simulation allows manufacturers to fully explore different opportunities, including lightweighting, within automotive designs before committing to physical prototypes.
Indeed, advanced visualisation tools allow OEMs and high-tier suppliers to create and analyse more design iterations, faster and also review them more quickly and thoroughly. They also enhance collaboration amongst teams, since individuals in different office can access the same design via a computer or in a virtual reality (VR) studios.
Advancements in the quality of VR technology and workflows allows designers and engineers to make better-informed decisions virtually. They can explore more options and design variations at full scale before physical models are prototyped. This reduces the wastage that comes with manufacturing prototypes, but also improves remote collaboration between teams. Equipped with the right tools, teams can review and provide feedback faster on the virtual models, without the need to travel. By reducing costs associated with physical prototyping, time and travel, VR can help manufacturers reduce wastage in manufacturing, as well as drive efficiency and speed.
Automating the mundane to boost innovation
Time to market cannot be sped up without the use of advanced CAM software and systems.
In order to deliver the best, most usable results, even the most advanced visualisation and simulation software requires input that accurately represents the design as it will be engineered and produced.
The problem with development and the iterations of designs is that each one is different. While individual development lines may carry over many features of the previous model, they will have modifications, lose some features and gain some from other, abandoned development lines.
Recreating the features that are to be carried over even before new attributes are added is time-consuming, repetitive and far from the optimum use of highly-qualified engineering designers’ and programmers’ skills.
This is where feature recognition in CAM can help. Instead of having to programme a part stage-by-stage, a feature-based programme enables the operator to programme parts using features that represent everyday shop terms, such as ‘hole’, ‘boss’, ‘pocket’, ‘turn’, ‘bore’ and so on. This programme is intelligent enough to recognise needs and requirements from these features and will automatically select the required tooling and operations without having to be instructed by the programmer.
Having the capacity to automatically recognise common features in a single workflow enables faster programming.
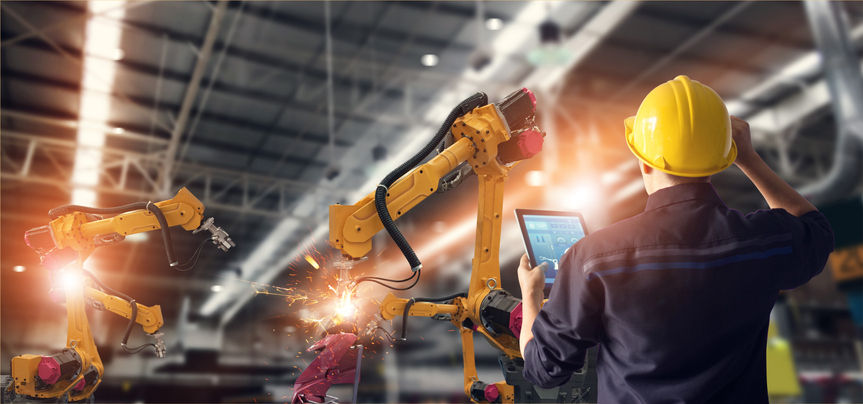
Automation takes care of the repetitive and mundane tasks, allowing the programmer to be more productive and use their time for higher-value tasks.
Looking to the future
The drive to cut time to market is unrelenting. Manufacturers along the breadth of the automotive supply chain must therefore work to shorten cycle times and meet customer demand, while doing so in a cost-effective manner.
New technologies and the data they generate will reduce the need to repeat adopted design features, time after time, from iteration to iteration. Not only that, they will also help to address skills shortages by enabling one highly skilled designer to lead teams of less-qualified people, bringing them up to speed and effectiveness quickly.
Disruptive technologies are now changing the manufacturing landscape in a way that will establish clear differences between those who embrace the opportunities and those who take their time before adopting them. So, which one will you be?
Water Sector Talent Exodus Could Cripple The Sector
Maybe if things are essential for the running of a country and we want to pay a fair price we should be running these utilities on a not for profit...