With the UK's digital manufacturing landscape best described as patchy, our panel agreed that cross-sector collaboration will be key to encouraging more widespread uptake
BAE's Julia Sutcliffe said there is a keen awareness of this in the aerospace sector. "One thing that is widely recognised is the vast amount of investment that’s going into things like digital technologies outside of the defence aerospace sector. It’s colossal globally. So without doubt, there is an incentive to ensure that we understand how and where it might fit,” she said.
In order to achieve the knowledge-sharing required, AMRC’s Colin Sirett said that industry needs to be proactive about creating environments where different sectors come together. He pointed to a recent digital forum convened by the AMRC, involving JCB, Jaguar Land Rover, Rolls-Royce, Marshall Aerospace and Defence Group, and Airbus. He said: “Out of that roundtable, there have been so many offshoots into different areas, where people have said, ‘Wow, I didn’t realise that was how you approach things.’ If you put the different sectors together, they thrive.”
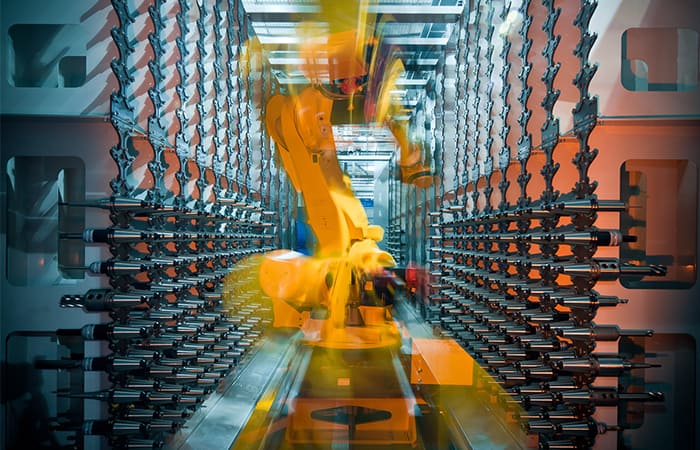
Paul Perera cited a recent visit to a medical company as evidence of the value of looking to other sectors. “I looked inside the factory windows and there were 150 additive machines spread out in front of me. I’ve seen nothing of that scale in aerospace. We’re looking at another industry with the scaling capability that we can only imagine. We need to excite our supply chain about the possibility of using this technology,” he said.
Perhaps one of the keys to enabling this common understanding lies with the suppliers. “We can certainly help, because we are connected with all these different sectors and we’re aware of what’s going on,” said ABB’s Mike Wilson. However, he warned that organisations’ reluctance to discuss areas of competitive advantage can make this difficult. "There are sometimes challenges because companies think, 'we develop this and we don't want anyone else to have it' and so we can't spread the gospel as much as we'd like."
Wilson stressed that it is important for bigger businesses to take the lead and work harder to spread the message down through the supply chains. "Without the whole environment collaborating on it, we still end up with these pockets of different groups of people that are keen, talking to each other and not making much of a concrete difference,” he said.
Simon Keogh agreed and added that, with the UK’s digital expertise dispersed across pockets in different sectors, suppliers have a vital role to play. “There are really great examples where people are using digitalisation, but it's so diverse,” he said. “They are just pockets here and pockets there. Right now, we’re finding that naturally leads to trying to use references that are outside of one industry for another industry.”
Sophie Jones said by looking further afield, manufacturing businesses can help solve challenges in other sectors and open up new markets. “One of the things we’ve tried to do as a business is look at industries that aren’t typically involved in additive manufacturing, because we think there’s enough attention on aerospace and enough potential in automotive,” she said. An example of this, she said, is her firm’s work in the quantum sensing field. “We went to them and said, ‘We can use AM to make your components better’, and everybody we spoke to said, ‘Not a chance. You can’t put AM components under ultra-high vacuum conditions and get them to perform’. So, we did exactly what they said we couldn’t do, and we opened up avenues within that industry that were categorically closed off to us. I think that’s a really interesting space to play in: working with people who typically you wouldn't talk to.”
Case study: In the wings
GKN is to open a new Global Technology Centre (GTC) in Bristol in 2020, where it will make concrete its commitment to digital manufacturing technologies. Costing £32m, the 10,000m2 facility will serve as a base for GKN Aerospace’s technology partnership in the Airbus Wing of Tomorrow programme. Its 300 engineers will focus on additive manufacturing, advanced composites, assembly and Industry 4.0 processes.
The centre will include collaborative space for R&D with universities, the UK Catapult network, and GKN Aerospace’s UK supply chain. Chief executive Hans Büthker said: “The GTC will ensure we continue to develop new technologies that deliver for our customers, making aircraft more sustainable and economical.”
Announcing the opening, the secretary of state for business, energy and industrial strategy, Greg Clark, said: “As the [aerospace] sector moves towards a cleaner, greener and more efficient future, we are partnering with industry through our modern Industrial Strategy and new Aerospace Sector Deal to ensure we have the skills, innovation and supply chain to continue our world leadership in aviation.” Among the GT collaborators is Additive Industries, the additive manufacturing hardware vendor, which is hoping to accelerate industrialisation of 3D-printed aerospace applications.
GKN has already found advantages with additive manufacturing through partnership with Stratasys, via which it is producing tooling, jigs and fixtures using the fused deposition modelling (FDM) technique. The company invested in an F900 FDM machine, with which it prints parts from Ultem 1010 (polyetherimide) thermoplastic resin. It takes around three hours to produce a part.
“This saves critical production time and, by printing in engineering- grade thermoplastic, we can produce 3D-printed tools with repeatable, predictable quality every time,” said additive manufacturing centre manager Tim Hope. “All the while matching the quality of traditionally produced tools and reducing the costs and concessions compared to equivalent metallic tooling.”
Additive techniques will be further used in the Prometheus programme, which will see the manufacture of a demonstrator for a low-cost reusable rocket engine using methane propellant, with the turbines generating power for the methane fuel system.
Manufacturing will take place at GKN Aerospace’s engine systems centre of excellence in Trollhättan, Sweden, with ArianeGroup the prime contractor.
UK Enters ‘Golden Age of Nuclear’
The delay (nearly 8 years) in getting approval for the Rolls-Royce SMR is most worrying. Signifies a torpid and expensive system that is quite onerous...