Hydrogen sensor
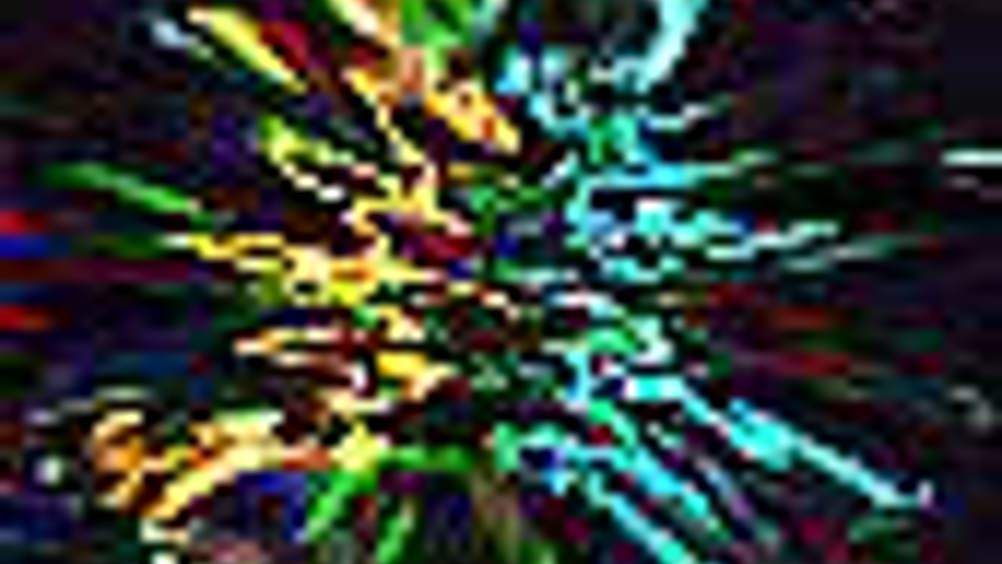
The same kind of chemical coating used to shed rainwater from aircraft and automobile windows also dramatically enhances the sensitivity and reaction time of hydrogen sensors.
The discovery was made by a team led by Zhili Xiao, a physicist in the Materials Science Division at the US Department of Energy's Argonne National Laboratory and an associate professor of physics at
The scientists demonstrated that the enhanced sensor design shows a rapid and reversible response to hydrogen gas that is repeatable over hundreds of cycles. A report on the team's research was published in May in Applied Physics Letters.
The sensor material is made by depositing a discontinuous palladium thin film on a glass slide coated with a grease-like self-assembled monolayer of siloxane anchored to the surface.
"By adding the siloxane self-assembled monolayer, we have changed the thin film dynamics," said Michael Zach, a chemist and holder of the Glenn Seaborg Postdoctoral Fellowship at
Register now to continue reading
Thanks for visiting The Engineer. You’ve now reached your monthly limit of premium content. Register for free to unlock unlimited access to all of our premium content, as well as the latest technology news, industry opinion and special reports.
Benefits of registering
-
In-depth insights and coverage of key emerging trends
-
Unrestricted access to special reports throughout the year
-
Daily technology news delivered straight to your inbox
Water Sector Talent Exodus Could Cripple The Sector
Maybe if things are essential for the running of a country and we want to pay a fair price we should be running these utilities on a not for profit...