As director of one of the world’s leading additive manufacturing (AM) research groups Nottingham University’s Professor Richard Hague is a central figure in the global AM research community.
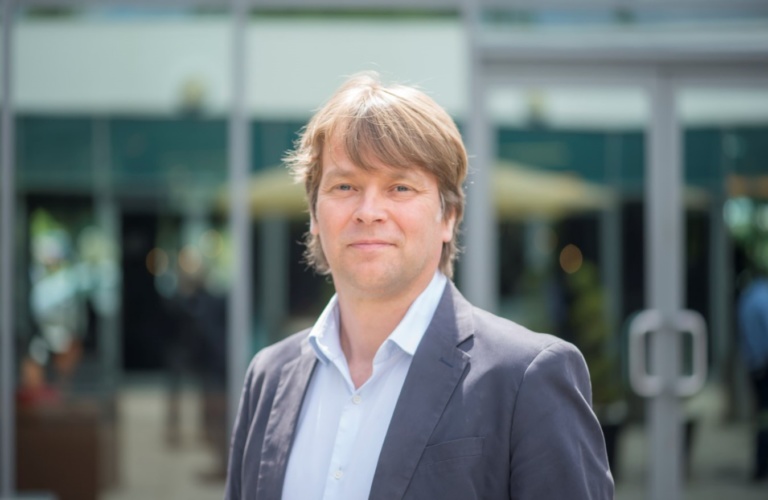
As previously reported by The Engineer, his team has played a key role in advancing understanding of how to exploit the design freedom enabled by additive techniques, an understanding that has helped inform industrial applications of the technology.
But Hague’s 100 person strong group, which since Dec 2018 has been based in a sparkling new facility within the university’s £24 million Advanced Manufacturing Building, is now pushing the envelope even further by exploring and developing the materials and processes that could ultimately enable engineers to print functional components in one shot, unlocking the potential of the technology across an ever-widening range of application areas.
More on additive from The Engineer
Q&A Feature: what's new in additive?
“We’re pretty good at the design side of things, we can create all of these fantastic structures and do topology optimisation,” he told The Engineer. “But the key thing is the material. The major expression of design freedom is in added functionality, so in many respects we’ve become a functional-materials for additive group.”
Hague’s lab boasts a broad and eclectic mix of technologies aimed at addressing this: a blend of systems - unlikely to be found anywhere else in the world - that ranges from nanoscale lithography devices and exotic purpose built research machines able to jet liquid metal, through to the chemical and analytical facilities required to develop and test promising new materials.
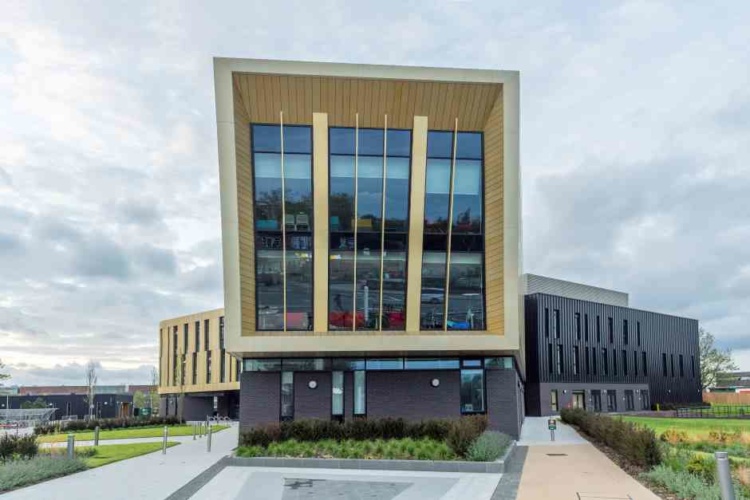
But during a recent visit to the centre, our first port of call was in more familiar territory, a collection of single metal laser sintering machines of the kind found throughout industry.
These systems are being used to test and explore a new generation of metallic materials optimised for AM. “In the metal powder bed processes most of the commercial materials available have been designed for other processes,” explained Hague, “for example, the aluminum silicon materials are casting materials and Ti64 is a wrought material. They haven’t been tailored for additive.”
Because of this, he said, these materials have shortcomings when used for additive processes. “The SLM process is effectively micro casting, you’re melting and solidifying, but the time scales involved are much shorter, so you get different microstructures that come out of the processing and therefore different mechanical properties. Normally the tensile and compressive strength are comparable but typically you get worse fatigue.”
Alongside trials of proprietary versions of existing materials, this area of the lab is also exploring the use of more exotic materials. One project, for instance, is looking at the challenges of additively manufacturing permanent and non-permanent magnetic materials. The ability to topologically optimise such materials and tailor the magnetic field could ultimately enable engineers to 3D print highly efficient electric motors, said Hague.
The group’s addressing a related challenge for single material polymer sintering systems where, said Hague, the development of materials with the right properties is even more challenging. “It’s much more difficult to get polymers in a powder form,” he said. “Broadly you melt metals, spray them, and they turn into little droplets, then you can sieve them and create powders. You can’t do that with polymers. You need to find different methods of creating the particles at the polymerisation stage – and that is challenging.”
Whilst research in these areas will ultimately help improve the utility of existing processes, the centre’s most groundbreaking and exciting work is arguably in the field of multiple and functional materials.
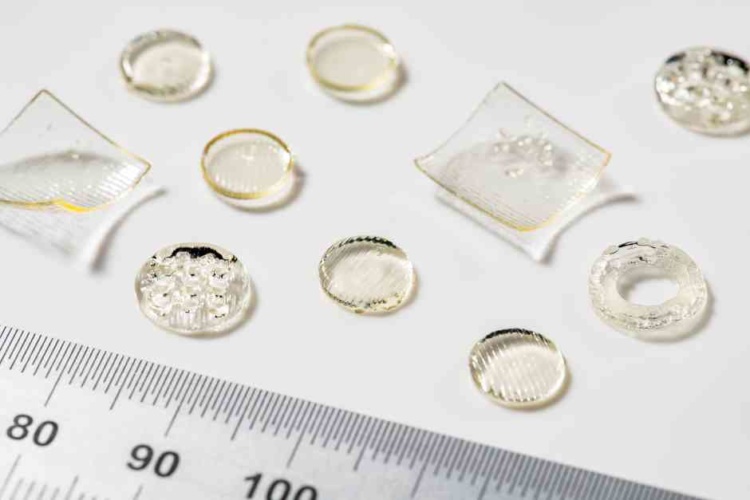
Much of its research here is based around the use of modified ink-jetting technologies, where systems equipped with multiple jetting heads are used to simultaneously deposit different materials onto a build platform.
A key area of interest is using this technology to jet so-called loaded materials. One example shown to The Engineer was a jetted silicone material containing nanoscale semiconductors that fluoresce when stimulated by light. Such devices could, said Hague, form the basis of future sensors for detecting changes in temperature or even the presence of pathogens such as viruses.
Another promising application is in-situ polymerisation, where droplets of monomer and catalyst are jetted, collided together and polymerised on the substrate. Hague said this approach could be used to create polymers with a higher molecular weight (often desirable from an engineering point of view) than other additive polymers.
The team is also exploring the area of metal-jetting, which is something of a holy grail for additive researchers around the world. Here, it is using the so-called MetalJet machine, an experimental system developed by inkjet specialist Oce (part of Canon), that is able to jet individual droplets of different metals at temperatures of up to 2000 degrees C.
Hague said that whilst ultimately such systems open the possibility for printing entire electronic components, the research is currently focused on the fundamentals of fusing materials together, and the impact that a host of different parameters – such as temperature, droplet velocity and droplet size can have on this process. “At the moment we’re not interested in making shapes, we’re much more interested in understanding how you jet a range of different materials and how you interface those different materials,” he said.
Alongside the fundamentals of the techniques, another key area for the group is in materials development and analysis. There are, explained Hague, a relatively small number of materials available for additive manufacturing, and expanding the range of materials is a key priority if the technology is to fulfil its potential.
A key capability here is an automated pick and place pipetting system, adapted from technology used in the pharmaceutical industry, that the team is using to screen new materials for jetting.
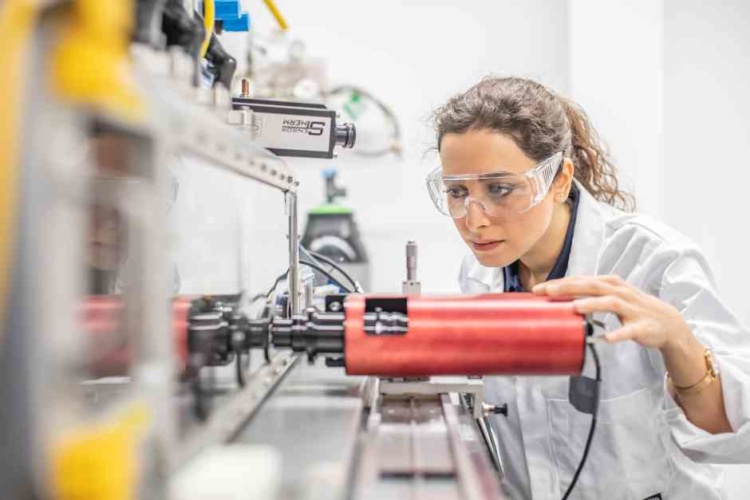
Analysing the rheology, surface tension and viscosity of new materials to see whether they are suitable for jetting is a time-consuming process that can take up to three hours for just a single material, explained Hague. The new system has turbocharged this process, enabling the team to test around 96 materials in just a couple of hours. “It’s like chucking a bunch of material at a wall and seeing which ones stick,” he said. “We’re taking a broad-brush approach for materials screening so we can determine whether we think something’s in the printable range.”
He added that the group is now looking at whether similar techniques could be applied to other liquid polymer systems, and even potentially metals.
The centre’s ability to target so many different research areas is thanks, in no small part, to its diverse and cross-disciplinary nature. Hague self-deprecatingly refers to himself as the “lowly mechanical engineer” in a team of physicists, material scientists, chemists and other specialists. Where necessary, the team is also able to draw on the wider expertise available elsewhere in the university as well as externally. “We’re a big group, with broad capability but we like to collaborate,” said Hague.
This cross-disciplinarity is particularly evident through the centre’s work in the healthcare and pharmaceutical sectors, a rapidly growing area of research which is seeing it work alongside some of the biggest names in pharma (Astrazenaca, Pfizer, and GSK to name just a few) on the applications of AM to technologies including tailored pharmaceuticals, electroceuticals and biosensors.
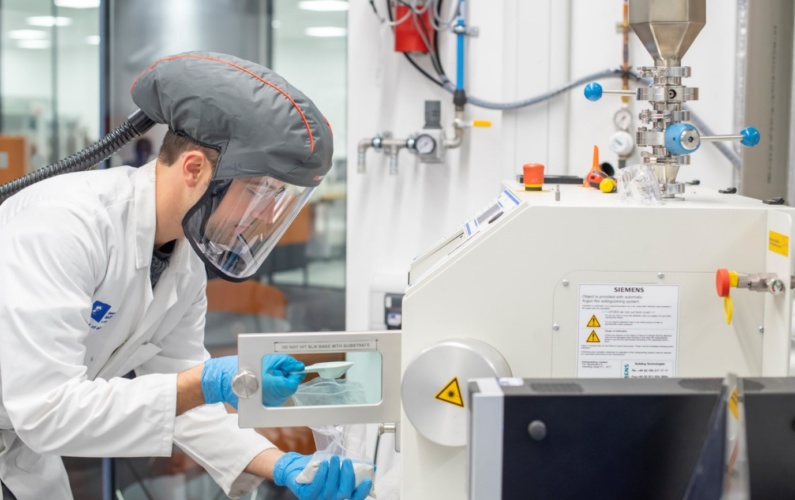
For Hague, who began his academic career firmly focused on the industrial applications of additive technologies, this ever-widening range of application areas fuels an infectious enthusiasm for an area of technology that continues to shape our world in unexpected and fascinating ways. “My job enables me to see things that most people only dream of seeing. It gives me access to industry and research that I never thought a boy from Suffolk would get to work in! It’s a bit of a dream, if you’re a tinkerer, like I am, it’s an absolute privilege”
Water Sector Talent Exodus Could Cripple The Sector
Maybe if things are essential for the running of a country and we want to pay a fair price we should be running these utilities on a not for profit...